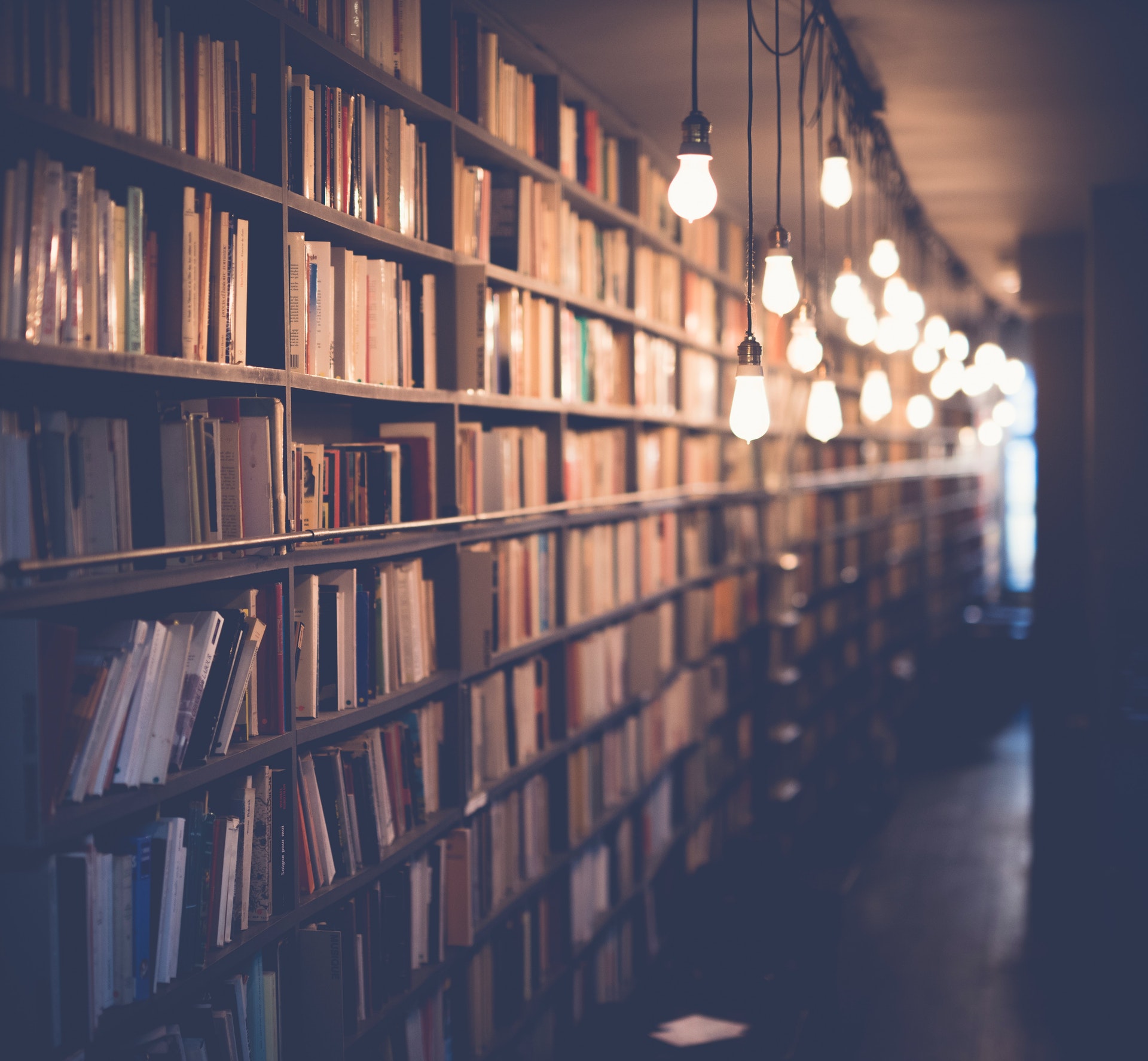
If you’re looking to buy metal for welding, there are a variety of places you can purchase this material from. Depending on the type of metal you require, marketplace options may include local hardware stores or large industrial supply companies.
Local Hardware Stores - Your local hardware store can be a great option for purchasing metal for welding projects. Sampling of metals may be limited but staples such as steel and aluminum can generally be found in various sizes at competitive prices. These stores also offer various properties and grades, allowing customers to compare different types of metals side-by-side.
Online Retailers - Online retailers provide a convenient way to shop for virtually any type or size of metal from the comfort from our own homes. It pays to shop around, as there are numerous vendors available that specialize in selling sheet metals and bars made out of different types like copper alloys, stainless steal and titanium just to name a few.. Additionally, if you need very specific dimensions or shapes that aren’t commonly found at traditional retail outlets – specialty vendors might have exactly what you need while other websites offer custom order options through their design platforms with quick turnaround times.
Industrial Supply Companies - Large industrial supply companies have been an invaluable resource when it comes to stocking shop supplies and hard-to-find materials including metals required for welding jobs – typically in bulk sized packages requiring upfront investments but offering discounted pricing compared to traditional retail outlets which is why many professional fabricators prefer going directly through these sources rather than visit physical/online retailers especially when dealing with larger scale projects on a regular basis. Many major brands such as Grainger carry hundreds products per item category ranging from thin gauge sheet stock all the way up thick structural plates and rods; making them one go shopping destination across most manufacturing industries
No matter where decide purchase your welding supplies from, it's always best practice compare experienced vendors price structure closely trade explore better deals between them so long run save some cash completion project efficaciously time frames desired outcome.
For another approach, see: Expanded Metal
What are the best places to buy metal for welding?
If you're looking for the best places to buy metal for welding, we've got you covered! Whether you have a big project or a more specific fabrication task in mind, there are some great sources out there to provide the exact materials your project needs. Here are some of our picks for the best places to buy metal for welding:
1. Online Metal Supply: Boasting one of the most comprehensive selections of metals in variety shapes and sizes, their inventory includes everything from aluminum and copper to stainless steel, carbon steel and even galvanized metals. On top of that, they offer an easy-to-navigate website so finding the right piece is a breeze.
2. Hardware Stores: Many local hardware stores have wide arrays of rods and sheets that come in many forms - perfect for any welding job! While they may be on the pricier side than online suppliers, they are advantageous because they allow shoppers to compare materials side by side with minimal effort.
3. Scrap Yards & Steel Mills: While these destinations aren’t as widely available as hardware stores or retailers online, scrap yards or steel mills can be great resources if you want inexpensive materials that don't necessarily need precision cutting or finish work done on them afterward (such as when fabricating help pieces). However shopping here does require extra labor due to sorting out usable material from unsuitable pieces before taking them home with you - making them better suited for heavier projects where small details don’t matter too much about source material condition.
At the end of it all it all boils down personal preference- whether going with convenience (hardware stores), affordability(scrapyards/steel mills),or selection (Online Metal supply) shoulld ultimately depend on individual project needs but regardless hopefully this list will provide plenty enough options when shopping around!
On a similar theme: When Did I Buy This Phone?
What type of metal is best for welding?
When it comes to welding, not all metal is created equal. Depending on your projects and desired results, certain types of metal may be better than others when it comes to welding. The type of metal you should use for welding ultimately depends on what type of weld strength you want the metal to have and how much heat the weld needs.
The most commonly used metals for welding are aluminum, stainless steel, low-carbon steel, copper alloys, and magnesium alloys. Of these metals, low-carbon steel is widely considered to be best because it has a higher melting point than most other metallic components used in fabrications and manufacturing processes. This means that the welds formed using low-carbon steel remain strong even with significant heat exposure. Low-carbon steel is also easy to form into complex shapes which makes it great for more intricate fabrication jobs such as building a car frame or constructing large structures such as bridges.
Stainless steel is another excellent option when it comes to welding because it resists corrosion longer than most metals do due to its high chromium content which helps protect against rusting and weathering over time making it great for marine applications or any job requiring long lasting parts in harsh environment conditions. Additionally its nonmagnetic properties make stainless steel ideal for medical implant work where magnetic fields can interfere with accuracy during surgery or imaging scans.
Aluminum can also be used when welding depending on the job but generally requires more attention particularly in regards temperature control during fabrication as aluminum melts at significantly lower temperatures than other metals meaning that too much heat could cause structural damage before adequate joining strength has been achieved between two sheets of aluminum material during brazing process. Lastly copper alloys are increasingly becoming popular due their unique malleability making them great for forming intricate shapes that require very goss detail when compared other lightweight metals.
Overall there many different types of metals suitable for fabricating complex products through metallic bonding process however if we had pick one best overall option real winner would undoubtedly be low carbon steal simply due its durability tensile strength stability over time under exposure extreme temperatures pressures making prime candidate choice any fabrication project requires longevity lifespan results without sacrificing safety integrity look finish desired end product.
Consider reading: When Should I Buy Bitcoins
What are the prices for purchasing metal for welding?
If you’re in the market for metal for welding, you need to know what to expect when it comes to pricing. After all, with several types of metals available, metal prices can vary greatly depending on quality and type. Factors like size and shape of your metal pieces play a role as well.
When it comes to welding metal, one of the most cost-effective options is mild steel plate and round stock. Mild steel plate is typically sold in 4’ x 8’ sheets – with gauges ranging from 16-10 – that cost between $70 and $335 per sheet (depending on thickness), while 1” round stock starts at around $1 per foot (with discounts for larger volumes). For example, 1/4" x 4' x 8' mild steel sheet runs about $200/sheet; whereas 1" x 12' rounds can be bought for around $12 a foot.
More specialized metals used for welding purposes are aluminum or stainless steels which tend to be slightly more expensive than regular mild steel at roughly double the cost per ton -- but their unique characteristics make them ideal for certain applications like food processing or biomedical equipment manufacturing needs. For instance, 6061 Alloy Aluminum Square Tubing costs about 75 cents a pound; while 304 stainless steel angle shafts can start at approximately $3/pound depending on size (+/-2$).
Overall, when selecting metals for your welding projects make sure you consider both quality requirements as well as pricing factors in order determine which would present the best value relative to your specific needs-- that said; greater buying power can often result in discounted rates so remember always ask around ahead of making any purchasing commitments!
For more insights, see: When to Buy Gold
What safety precautions should I take when welding metal?
When welding metal it is important to take several safety precautions to ensure that you can work as safely as possible. The following are some key precautions to keep in mind:
1. Wear proper protective gear – When welding, it’s essential that you wear the correct personal protective equipment, such as a welding helmet with a full face shield, and flame retardant clothing. This will help protect your skin and eyes from burns or exposure to sparks while welding.
2. Keep your workspace clean – It is also very important to make sure your workspace is free of clutter and combustible materials before beginning any welding process. Be sure all tools are put away correctly and nothing flammable is near the area of space where you’re working with an open flame or electrode arc welder.
3 Secure your materials – Make sure that all of the material you’re using for welding is securely bolted or clamped down so it won’t move during the process which could result in harm from hot metal flying off unexpectedly or even cause an arc flash incident due to inadequate grounding of metals in contact with each other.
4 Check air quality – Welding can produce fumes which may contain hazardous chemicals or toxic particles, so ensure you check the air quality before starting a job; exhaust systems should be installed if necessary for better airflow within enclosed workspaces like shops or garages that lack natural ventilation sources such as open doors/windows etc..
5 Don't weld near gasoline -Be mindful not to weld near areas containing substances like gasoline evaporators due to risk of fire hazards caused by heat ignition oil droplets in close proximity when sparks fly could lead into greater explosions if proper care isn't taken.
Following these basic guidelines when working with metal fabrication can greatly reduce potential risks associated with the craft which will allow one peace of mind when getting into this type activity!
You might like: Buy Weld Crete Bonding Agent
What size pieces of metal should I use for welding?
When considering what size metal pieces to use for welding, there are several factors that will impact your decision. To figure out the best size pieces of metal to use for specific welding projects, it is important to consider the type of weld that is necessary, the thickness of the metal material being used, and how much access you have to larger pieces.
The type of weld needed will dictate what size pieces should be used. For example, a fillet weld requires less access than other types of flat and groove welds. In these cases smaller pieces are generally necessary in order to get into tight spots and ensure proper penetration during the process. On the other hand for flat or groove-type joints with sufficient access larger sizes can be employed resulting in stronger bonds with less time spent in setup and positioning than that required by smaller pieces.
The thickness of material also affects what size parts should be used when welding; thicker materials often require more area for connecting than thinner materials do so using larger size metal may make sense in these cases as it reduces overall preparation time on both ends when compared with using more narrow strips or sheets.. Along those same lines if a small gap between two metal components needs filling then small strips might make more sense as they can easily fit into any existing voids allowing greater control over placement accuracy and ensuring a complete seal upon joining completion.
Ultimately finding – or fabricating - the right sized piece of metal boils down to finding something that is large enough provide room work comfortably but not so big that it requires an excessive amount of prepping before starting up your welder or creates an awkward aesthetic appearance afterwards once complete - unless you're specifically trying for a certain look right? As such assessing all relevant factors prior to beginning will help ensure you select compatible sizes for excellent results without lots unnecessary hassle!
Take a look at this: Metal Siding
What tools should I have to weld metal properly?
Welding metal is an essential skill for any fabrication project, so having the proper tools makes a huge difference in the quality of your work. With the right equipment and knowledge, you can create strong joints that will last for years.
For basic welding projects, you’ll need these essential tools:.
1) A welding machine – In order to weld metal properly, you need a reliable power source that includes adjustable settings based on your material selection. Look for welders with accurate amperage control and settings like stick/MMA or TIG/MIG relevant to your project.
2) Safety gear – Protect yourself by wearing safety glasses and a flame-resistant hood during welding activities; consider adding protective sleeves and gloves for additional coverage. You might also want to keep a fire extinguisher nearby just in case sparks fly onto other materials!
3) Quality consumables – Consumables like electrodes, filler rods and nozzles start to break down over time; make sure they are always well-maintained so they perform optimally when used. Better yet, use disposable items whenever possible to avoid potential slag build up in hard-to-reach areas.
4) Accessories – Having cutting jigs helps ensure clean cuts while clamps provide safe hands free operation during extended use situations; look into other helpful gadgets such as grinders that allow changes easily made minor adjustments between applications..
5) Aluminum MIG Welding Wire - In most cases aluminum MIG wire should be used when welding aluminum sheets together such as body panels plus more light gauge parts where extra strength isn't required. The aluminum wire tends to have better melting characteristics than mild steel wires which gives better overall results with minimal risk of warping due from increased heat input scattered around creating irregularities on finished surface. Its very important not mix metals when using MIG or Tungsand Arc techniques because it can cause certain reaction resulting corrosion in future, thus ruining entire projects.
Having these core supplies ready will giveyou the confidence and tools neededto completea successful weld job withstrong joints built t o last!
Sources
- https://www.theweldingarc.com/where-to-find-metal-for-welding/
- https://www.youtube.com/watch
- https://welderslab.com/what-is-the-cheapest-metal-for-welding-projects
- https://www.aafrc.org/welding-safety/
- https://toolblogtalk.com/where-to-buy-metal-for-welding-projects-or-to-practice-on/
- https://weldingmastermind.com/how-to-weld-tool-steel-10-tips/
- https://www.theweldguru.com/buy-metal-for-welding/
- https://www.metalsupermarkets.co.uk/the-best-metals-for-welding/
- https://weldersgalore.com/safety-precautions-in-welding-what-you-need-to-know/
- https://forum.millerwelds.com/forum/welding-discussions/33449-welding-table-top-material-choice-and-thickness
- https://safetyculture.com/topics/welding-safety/
Featured Images: pexels.com