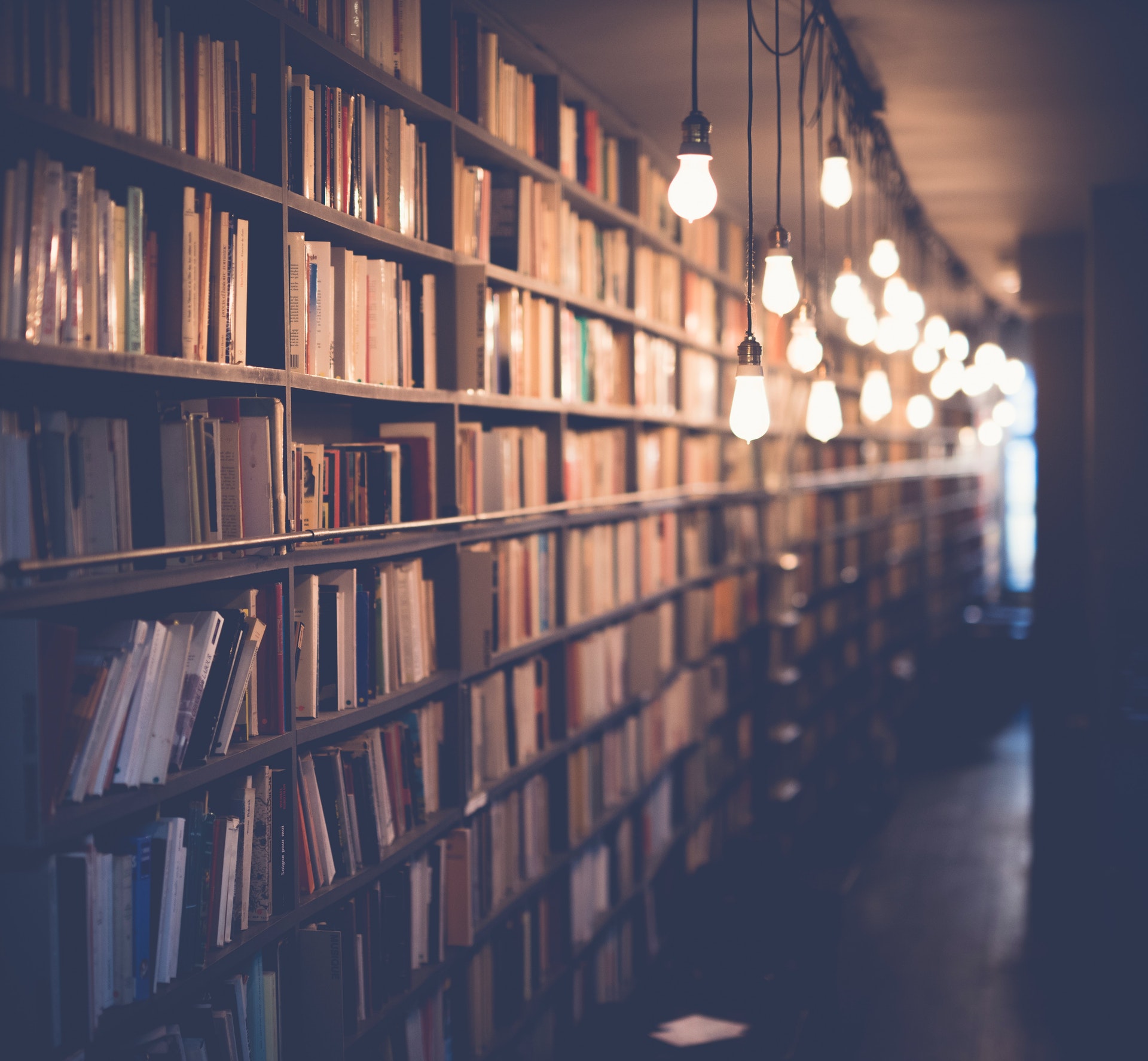
In welding, the undercut is a groove created along the edge of the base metal that is perpendicular to the weld line. This groove is created by the heat of the welding arc and is typically deeper on the side of the weld where the arc is striking the base metal.
The undercut serves two main purposes in welding. First, it provides extra space for the weld metal to bead up into. This helps to create a stronger weld joint by giving the weld metal more room to expand into as it cools and contracts. Second, the undercut strengthens the weld joint by creating a mechanical interlock between the weld metal and the base metal.
While the undercut is an important part of the welding process, it can also be a problem if not done correctly. If the undercut is too deep, it can weaken the base metal and cause the weld to fail. If the undercut is too shallow, it can leave the weld joint susceptible to cracking.
Thus, it is important to control the depth of the undercut when welding. The welder must have a good understanding of the welding process and the correct techniques to ensure that the undercut is of the correct depth.
For your interest: Give Standing Spray Depth
What is an undercut in welding?
In welding, an undercut is a groove or notch that is cut into the base metal along the edge of the weld. This groove is typically cut with a gas-powered cutting torch, but can also be machined with a milling machine or a router. The purpose of the undercut is to create a mechanical joint between the weld and the base metal. The undercut also provides additional metal for the weld to adhere to, which increases the strength of the weld.
While the undercut is typically cut into the base metal before welding, it can also be cut into the weld metal after welding is complete. This is known as a post-weld undercut and is often used to remove defects from the weld or to improve the appearance of the weld.
The depth of the undercut is typically between 1/16” and 1/8”, but can be deeper if necessary. The width of the undercut should be equal to the width of the weld bead. Un dercuts that are too wide or too deep can weaken the weld and cause it to fail.
The most common type of undercut is the V-groove, which is created by cutting two parallel lines into the base metal that meet at a point. This type of undercut is easy to create and provides a strong mechanical joint between the weld and the base metal.
Another type of undercut is the U-groove, which is created by cutting a single, wide groove into the base metal. This type of undercut is more difficult to create, but provides a stronger joint between the weld and the base metal.
Undercuts are an important part of welding and should be used whenever possible to create a stronger weld. When cutting undercuts, be sure to use the proper width and depth for the weld bead that will be used. too much or too little undercut can weaken the weld and cause it to fail.
A fresh viewpoint: Width Ski
What causes an undercut in welding?
Undercuts are a welding defect that can occur for a variety of reasons. The most common cause of undercuts is improper welding technique. Other causes can include incorrect torch angle, incorrect electrode size or type, and improper gas flow.
Undercuts can also occur when the base metal is not clean or when there is too much oxidation on the surface. This can happen when the base metal is not adequately prepared before welding, or when the welding environment is not clean enough.
If not properly repaired, undercuts can weaken the weld and make it more susceptible to cracking. In some cases, undercuts can also cause the weld to become detached from the base metal entirely.
Undercuts can be avoided by using the proper welding techniques, preparing the base metal correctly, and keeping the welding environment clean. If an undercut does occur, it can be repaired by welding over the defect with a properly sized electrode.
Suggestion: What Are the Best Places to Elope in California?
How can you prevent an undercut in welding?
When welding, an undercut is a condition that can occur if the heat used to melt the metal being joined is too high. This can cause the molten metal to flow into the joint between the two pieces being joined, weakening the joint. To prevent an undercut, the welder needs to use the proper welding techniques and equipment.
The welding process involves using heat to melt the metal being joined. If the heat is too high, the molten metal can flow into the joint between the two pieces being joined. This can cause the joint to weaken, and eventually fail. To prevent an undercut, the welder needs to use the proper welding techniques and equipment.
The welder should start by setting the power source to the correct setting. The power setting should be based on the thickness of the metal being welded. If the power setting is too high, the molten metal can flow into the joint and cause an undercut.
Next, the welder needs to select the right size and type of electrode. The electrode should be the same size as the metal being welded. If the electrode is too small, it can cause the heat to be too high and cause an undercut.
The welder also needs to select the right welding wire. The welding wire should be the same size as the electrode. If the welding wire is too small, it can cause the heat to be too high and cause an undercut.
The welder should also select the right type of welding gas. The welding gas should be the same type as the metal being welded. If the welding gas is too hot, it can cause the molten metal to flow into the joint and cause an undercut.
The welder should also use the right welding techniques. The welder should use a short, quick welding stroke. If the welder uses a long, slow welding stroke, it can cause the heat to build up and cause an undercut.
The welder should also use a low welding current. If the welding current is too high, it can cause the heat to build up and cause an undercut.
The welder should also keep the welding torch at a constant angle. If the welding torch is not at a constant angle, it can cause the heat to build up and cause an undercut.
The welder should also use a welding shield. The welding shield should be made of a material that will reflect the heat away from the weld. If the
For your interest: Romanesque Metalwork Pieces
How does an undercut affect the strength of a weld?
The undercut is a welding defect that can occur when the weld metal does not fill thespace between the two base metals. The undercut can occur on the top or bottom side of theweld and can be different sizes. The undercut can also be on one side of the weld or bothsides.
The undercut affects the strength of the weld because it creates a stress riser. Thestresses at the undercut can be very high, and this can cause the weld to fail. The undercutcan also make the weld more susceptible to cracking.
One way to reduce the undercut is to use a larger electrode. This will allow the welderto depositor more weld metal into the undercut. Another way to reduce the undercut isto use a higher welding speed. This will allow the weld to penetrate the base metal morequickly and fill the undercut.
Suggestion: Can You Use Bleach on Your Areola?
How does an undercut affect the appearance of a weld?
An undercut is a groove that is cut into the base metal around the edges of a weld. This groove is usually made by the welding torch, and it affects the appearance of the weld by making it narrower and less deep.
Undercuts can occur for several reasons. If the welding torch is not held at the correct angle, it can cut too deeply into the base metal. This will make the weld appear narrower and shallower. Another reason for undercuts is that the welding torch is not moved smoothly around the edges of the weld. This can also result in an uneven weld that is narrower and less deep.
Undercuts can also be caused by impurities in the base metal or the welding rod. If there are impurities in the base metal, they can weaken the weld and cause it to crack. If there are impurities in the welding rod, they can make the weld less strong and more likely to fail.
Undercuts can be corrected by grinding the weld down to the correct width and depth. This can be done by hand or with a power grinder. If the undercut is severe, it may be necessary to replace the section of weld.
welding
You might enjoy: Cut Vintage Postcard Scalloped Edges
How does an undercut affect the quality of a weld?
An undercut is a grove that is cut into the edge of a workpiece to prepare it for welding. The purpose of an undercut is to create a mechanical interlock between the workpiece and the weld. This interlock helps to prevent the weld from cracking and ensures the structural integrity of the weld.
An undercut affects the quality of a weld in several ways. First, it increases the amount of contact area between the workpiece and the weld. This increased contact area provides more support for the weld and helps to prevent cracking. Second, the undercut provides a keyway for the weld bead to follow. This keyway helps to ensure that the weld bead is properly formed and evenly distributed. Finally, the undercut helps to prevent the workpiece from sliding during the welding process.
The quality of a weld is also affected by the width of the undercut. A wider undercut provides more support for the weld and helps to prevent cracking. However, a too wide undercut can make it difficult to form a proper weld bead. The ideal width of an undercut for welding is about 1/16 inch.
A different take: Helps Enable
How does an undercut affect the cost of a weld?
The undercut is the depth of the groove made by the welding torch in order to control the penetration of the weld bead. The undercut affects the cost of a weld in two ways; first, it affects the amount of time required to make the weld, and second, it affects the amount of welding material required.
The amount of time required to make the weld increases as the depth of the undercut increases. This is because the welding torch must be moved more slowly in order to control the depth of the weld bead, and because the welding operator must be more careful in order to avoid making the weld too deep. The amount of welding material required also increases as the depth of the undercut increases. This is because the weld bead must be larger in order to fill the undercut, and because the amount of heat required to make the weld increases as the depth of the undercut increases.
The undercut affects the cost of the weld in these two ways; however, the effect on the cost of the weld is not proportionate to the effect on the time required to make the weld or the amount of welding material required. This is because the undercut also affects the strength of the weld. A deeper undercut results in a weaker weld, and a shallower undercut results in a stronger weld. As a result, the cost of the weld is affected not only by the time required to make the weld and the amount of welding material required, but also by the strength of the weld.
A fresh viewpoint: Welding Rod Oven
How does an undercut affect the safety of a weld?
An undercut is a groove or notch that is made in the base metal ahead of the weld that does not fill with weld metal. The groove is made by the removal of base metal by grinding, machining, or air carbon-arc cutting. The width of the undercut should not exceed 1/16 inch (1.6 mm) and the depth should not exceed the weld metal thickness. An undercut creates a lack of fusion at the root of the weld, and if not properly repaired, can act as a stress riser and lead to weld failure. In addition, an undercut can make it difficult to achieve a full penetration weld, which can also lead to weld failure. To repair an undercut, a welder will need to build up the root of the weld with weld metal, and then re-weld the area. This is a time-consuming and costly process, and it is often difficult to achieve a repair that is as strong as the original weld. For these reasons, it is important to avoid undercuts when welding.
Take a look at this: Sensor Failure
How does an undercut affect the efficiency of a weld?
An undercut is a groove made in the base metal behind the weld bead. It is usually made with an angle grinder fitted with a thin cutting wheel. The purpose of an undercut is to create a mechanical key between the two pieces of metal being joined, which gives the weld greater strength. It also helps to prevent the weld from adding too much material to the joint, which can make it weaker.
The downside of an undercut is that it can make the weld less efficient. The undercut creates a larger surface area for the weld to adhere to, which can make the weld take longer to cool and solidify. This can lead to problems with the weld's strength and integrity. In addition, the undercut can make it more difficult to achieve a good weld bead profile.
It is important to weigh the pros and cons of an undercut before deciding whether or not to use it. In some cases, an undercut can improve the efficiency of a weld, but in other cases it can have a negative effect. When in doubt, it is best to consult with a welding expert to get the best advice for your specific application.
Take a look at this: What Is Friction?
Frequently Asked Questions
What is a crown undercut in welding?
A crown undercut is a localized decrease in the thickness of the metal near a weld. This can result from several different things, including improper welding techniques, weak metal or even surface rust. When this occurs, heat and pressure will force the metal together, creating a stress crack at the weld junction.
How do you fix undercut in welding?
The most common way to fix undercut in welding is to reduce the current flow. You can also manipulate the heat input with a stick out of the electrode. The longer the stick out, the less heat it produces.
How to avoid undercut in MIG welding?
One way to avoid an undercut is by lowering the amperage.
What causes undercuts in Fillet welding?
There are a few reasons why undercuts may form in fillet welds. One reason is that the metal around the Joint is not of a thickness or quality sufficient to withstand the heat and stress of welding. Undercuts can also be caused by improperly placed electrodes, use of incorrect welding techniques or forcing too much heat into the joint causing distortion and weakening of the metal.
What is an arc in welding?
In welding, an arc is a self-contained fusion zone where the electrode and the material to be welded come into close contact. The heat of the plasma created by the electric arc melts the metal at the points of contact, creating a joint.
Sources
- https://waterwelders.com/what-is-undercut-in-welding/
- https://www.welderscare.com/how-to-prevent-undercut-in-stick-welding/
- https://sage-answer.com/how-do-you-prevent-undercut-in-tig-welding/
- https://www.materialwelding.com/welding-undercut-causes-remedies/
- https://short-facts.com/how-do-you-prevent-undercut-welding/
- https://prowelderguide.com/what-are-the-causes-of-an-undercut-weld/
- https://weldingzilla.com/undercut-in-welding/
- https://weldingtech.net/undercut/
- https://theweldingguide.com/prevent-undercut-welding/
- https://sage-tip.com/useful-tips/what-are-the-causes-undercut-welding-defect-and-how-do-you-prevent-it/
Featured Images: pexels.com