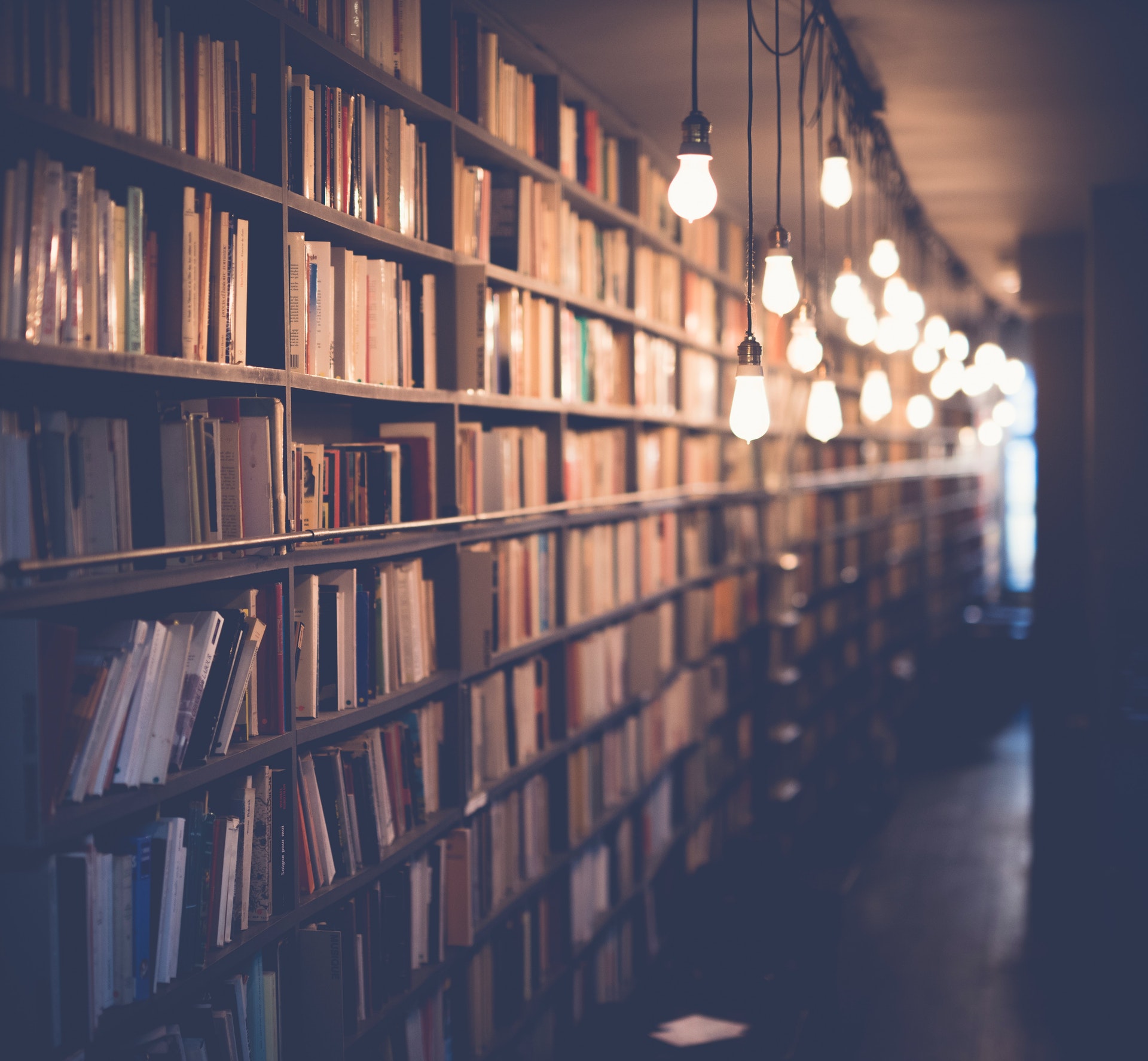
Cleanroom paper is a paper that is used in a cleanroom. A cleanroom is a room that has been designed to be as free of contaminants as possible. The walls and ceiling of a cleanroom are usually made of smooth, hard surfaces that can be easily cleaned. The floors are usually made of smooth, hard tiles that can be easily cleaned. There are also special HEPA filters that remove contaminants from the air.
Cleanroom paper is made of a material that is designed to not shed contaminants. The paper is usually white or off-white in color. It is also usually thicker than regular paper. Cleanroom paper is used in many industries, including the semiconductor industry, the pharmaceutical industry, and the food industry.
There are many different types of cleanroom paper. The type of paper that you use will depend on the application that you are using it for. For example, cleanroom paper that is used in the semiconductor industry is different than the paper that is used in the pharmaceutical industry.
Cleanroom paper is an important part of keeping a cleanroom clean. If you are working in a cleanroom, it is important to use the proper type of paper. If you are not sure which type of paper to use, you should ask someone who is familiar with cleanrooms.
What is a cleanroom paper?
A Cleanroom paper is a type of filter paper that is used to trap small particles and prevent them from contaminating surfaces or equipment in a clean room. Cleanroom papers are made from a variety of materials, including cellulose, polyester, and polypropylene. They are available in a variety of sizes and grades to suit different applications.
Cleanroom papers are used in a variety of industries, including electronics, pharmaceuticals, and food processing. They are also used in hospitals and other healthcare facilities to keep surfaces clean and prevent the spread of infection.
Here's an interesting read: Clean Paper Pellet Cat Litter
What are the benefits of using cleanroom paper?
A cleanroom is a room in which the air is filtered to remove contaminants and the surfaces are kept free of dust. Cleanrooms are used in a variety of industries, including semiconductor and pharmaceutical manufacturing, food processing, and hospitals.
One of the most important aspects of a cleanroom is the paper. Cleanroom paper is specially treated to be static-free and lint-free. It is also made from a material that does not shed fibers.
The benefits of using cleanroom paper are numerous. First, it helps to keep the cleanroom clean. Second, it does not add contaminants to the products being produced in the cleanroom. Third, it is strong and durable, so it can withstand repeated cleaning. Finally, it is available in a variety of sizes and colors to meet the needs of different cleanrooms.
Cleanroom paper is an essential part of any cleanroom. It helps to keep the cleanroom clean and free of contaminants. It is also strong and durable, so it can withstand repeated cleaning.
How is cleanroom paper different from regular paper?
Cleanroom paper is paper that has been specifically designed for use in cleanrooms. It is made with unique materials and construction that allows it to resist the buildup of static charges and to repel contaminants such as dust, dirt, and moisture. This type of paper is often used in the manufacturing of semiconductor devices, medical devices, and other sensitive products.
The most important difference between cleanroom paper and regular paper is the cleanliness of the finished product. Cleanroom paper is manufactured in a controlled environment where there is little to no chance for contamination. This results in a paper that is much cleaner and smoother than regular paper. In addition, cleanroom paper often has a lower background static charge and can resist higher levels of humidity than regular paper.
While cleanroom paper is generally more expensive than regular paper, it is worth the investment for any applications where cleanliness and contamination control are critical.
What are the guidelines for using cleanroom paper?
Most cleanrooms are classified according to the maximum number of particles allowed per cubic meter at a specified particle size. Classifications are often given as either Class 1, 10, 100, 1,000 or 10,000. In a cleanroom with a Class 1,000 classification, for example, there can be no more than 1,000 particles larger than 0.5 micrometers in any given cubic meter of air.
The goal of a cleanroom is to keep particulate levels as low as possible. The way that a cleanroom does this is by providing a controlled environment with filtration systems that remove particulates from the air.
There are a few things to keep in mind when using cleanroom paper. The first is that it is important to use paper that is certified for use in cleanrooms. This paper has been tested and approved for use in environments with low levels of particulates.
The second thing to keep in mind is that cleanroom paper should be handled with care. This paper is designed to resist tears and ESD (electrostatic discharge), but it can be damaged if it is mishandled.
When using cleanroom paper, it is important to follow the guidelines for your specific cleanroom. These guidelines will help you to maintain a clean and safe environment.
How should cleanroom paper be stored?
There are many factors to consider when determining how to store cleanroom paper. Some of these factors include the type of paper, the application it will be used for, and the specific cleanroom environment.
The type of paper is important to consider because different types of paper have different storage requirements. For example, static-dissipative paper must be stored in a static-free environment, while printer paper can be stored in a regular office environment. The application the paper will be used for is also important to consider. If the paper will be used in a critical application, such as semiconductor manufacturing, it is important to store the paper in a dust-free and moisture-free environment. The specific cleanroom environment is also important to consider. If the paper will be used in a class 100 cleanroom, it is important to store the paper in a class 100 cleanroom locker.
There are a few general guidelines that should be followed when storing cleanroom paper. The paper should be stored in a dry, dust-free environment. The paper should also be stored in a way that prevents it from being damaged or contaminated.
One way to prevent damage or contamination is to store the paper in a cleanroom paper bag. These bags are made of a static-dissipative material and are designed to protect the paper from dust and other contaminants. Another way to prevent damage or contamination is to store the paper in a cleanroom paper box. These boxes are made of a material that is resistant to static and are designed to protect the paper from dust and other contaminants.
When storing cleanroom paper, it is important to follow the guidelines that are specific to the type of paper and the application it will be used for. By following these guidelines, you can ensure that the paper remains clean and undamaged.
How often should cleanroom paper be replaced?
It is important to regularly replace cleanroom paper to maintain a safe and clean working environment. Depending on the application, cleanroom paper can last anywhere from a few hours to a few days. For example, in a semiconductor cleanroom, paper may only need to be replaced every few hours, whereas in a food manufacturing cleanroom, paper may last a few days. In general, it is best to replace cleanroom paper once it becomes visibly soiled or when it is no longer able to effectively clean surfaces.
What are the consequences of not using cleanroom paper?
The cleanroom paper is a specially treated paper that is used in laboratories and other environments where it is important to keep airborne particles to a minimum. The paper is treated with a number of chemicals that make it resistant to static electricity and help it to repel dust and other particles. The cleanroom paper is also usually white so that it can reflect light, making it easier to see any particles that may be present.
The main consequence of not using cleanroom paper is that there is an increased risk of contamination. If dust and other particles are able to settle on surfaces, they can easily be spread around the room and come into contact with sensitive equipment or experiment materials. This can lead to false readings or even damage to delicate equipment. In a worst-case scenario, contamination of a cleanroom environment can lead to a complete shutdown of the facility as procedures must be put in place to clean and decontaminate the entire area.
Another consequence of not using cleanroom paper is that it can be difficult to maintain a consistent level of cleanliness. If dust and other particles are able to settle on surfaces, they can eventually build up to the point where they are visible to the naked eye. This can make it difficult to assess the level of cleanliness in an environment and make it more difficult to achieve and maintain desired levels of cleanliness.
Overall, the consequences of not using cleanroom paper can be significant. Contamination risks increase, it can be difficult to maintain cleanliness, and false readings or damage to equipment can occur. If you are working in an environment where it is important to keep airborne particles to a minimum, it is essential to use cleanroom paper.
How can I ensure that my cleanroom paper is effective?
There are many factors to consider when ensuring the effectiveness of cleanroom paper. The type of paper, the size and shape of the room, the level of cleanliness required, and the number of people using the paper are all important factors.
The most important factor in ensuring the effectiveness of cleanroom paper is the type of paper. Different papers have different properties that make them more or less effective in different situations. For example, some papers are better at absorbing spills and keeping surfaces clean, while others are better at resisting tearing and abrasion.
The size and shape of the room also play a role in the effectiveness of cleanroom paper. If the room is small and square, the paper will likely be more effective than if the room is large and irregularly shaped. The level of cleanliness required is also a factor. If the room needs to be absolutely spotless, the paper will need to be able to withstand more cleaning and be replaced more often.
The number of people using the paper is also a factor. If there are many people using the paper, it will need to be replaced more often. If there are only a few people using the paper, it can last longer.
In general, the best way to ensure that cleanroom paper is effective is to choose the right paper for the job and to replace it often.
Worth a look: Demi Size Paper
What are the most common mistakes people make when using cleanroom paper?
Most people are not aware of the proper protocol for using cleanroom paper. There are many things to consider when using this type of paper, such as the cleanliness of the paper itself and how it will be used in conjunction with other materials. The following are the most common mistakes people make when using cleanroom paper:
Not all cleanroom paper is the same: Just as with any other product, there are different grades and types of cleanroom paper. Not all paper is created equal and it is important to know the difference before using it. The most common mistake is using the wrong type of paper for the desired application.
Using too much or too little paper: Another mistake is using too much or too little paper. It is important to use the correct amount of paper so that it effectively does its job without wasting valuable resources.
Not changing paper often enough: Depending on the application, cleanroom paper should be changed out regularly. Not changing the paper often enough can lead to cross contamination and other serious issues.
Not properly disposing of cleanroom paper: Once paper has been used, it needs to be properly disposed of in order to prevent cross contamination. This means placing it in the proper receptacle and following all protocol for disposal.
Ignoring protocols: There are specific protocols that should be followed when working in a cleanroom. These protocols are in place to ensure the cleanliness of the environment and to prevent cross contamination. Ignoring these protocols can lead to serious issues.
Not following the proper steps for cleaning: Cleaning a cleanroom is a delicate process that must be done correctly in order to be effective. There are specific steps that must be followed in order to properly clean a cleanroom. Not following these steps can lead to cross contamination.
These are just a few of the most common mistakes people make when using cleanroom paper. It is important to be aware of these mistakes so that they can be avoided. By following the proper protocol and taking the necessary precautions, cleanroom paper can be used effectively and safely.
Frequently Asked Questions
What are the rules and regulations of a cleanroom?
There are specific cleaning procedures that must be followed in a cleanroom in order to maintain the safety of personnel and materials. The following are the most important rules for a cleanroom: The walls, floors, and work surfaces should be regularly cleaned with standard cleaning agents and equipment. Any deposited dust or debris should be cleaned up immediately. Cleanrooms should be kept at a constant operating temperature.
What is the size of cleanroom paper?
The cleanroom paper is 8.5"x11" and has a weight of 22.5# LT-7177BE-8A-03
What is ECOBOND cleanroom paper?
ECOBOND cleanroom paper is a type of paper that is specifically designed for use in writing, copying, and printing within controlled environmental areas. ECOBOND cleanroom paper is made with the purest quality cellulose from specially selected forests, and it is specially coated to minimize particle and fiber release.
How do I order cleanroom paper online?
To order cleanroom paper online, you can click above, email [email protected], or call customer service at (303)752-0076.
What is the size of Criti cleanroom paper?
8.5″x11″ and 11″x17″
Sources
- https://cleanroomindustry.com/the-importance-of-using-cleanroom-documentation/
- https://www.linkedin.com/pulse/what-cleanroom-paper-lighthouse-worldwide-solutions
- https://www.cleanroomsupply.com/cleanroom-paper-p-6004.html
- https://www.rdm-ind.com/the-advantages-of-a-good-cleanroom/
- https://www.medcosupplies.com/blogs/news/how-to-properly-store-garments-for-cleanrooms
- https://cleanroomworld.com/cleanroom-documentation/cleanroom-paper
- https://cleanroomtechnology.com/news/article_page/Five_hidden_sources_of_contamination_in_the_cleanroom/201272
- https://www.cleanroomtechnology.com/news/article_page/How_often_should_I_validate_my_cleanroom_to_meet_ISO_1464412015/115090
- https://www.rdworldonline.com/when-should-cleanroom-garments-be-replaced/
- https://berkshire.com/cleanroom-vs-standard-paper/
- https://high-techconversions.com/what-materials-used-in-cleanroom/
- https://www.cleanroomtape.com/hidden-sources-of-contamination/
- https://www.golighthouse.com/en/blog/what-is-a-cleanroom-and-how-using-a-cleanroom-can-benefit-you-445
- https://us.vwr.com/store/product/4673042/vwr-pureimagetm-cleanroom-paper
- https://snco.com/every-cleanroom-needs-cleanroom-notebook/
Featured Images: pexels.com