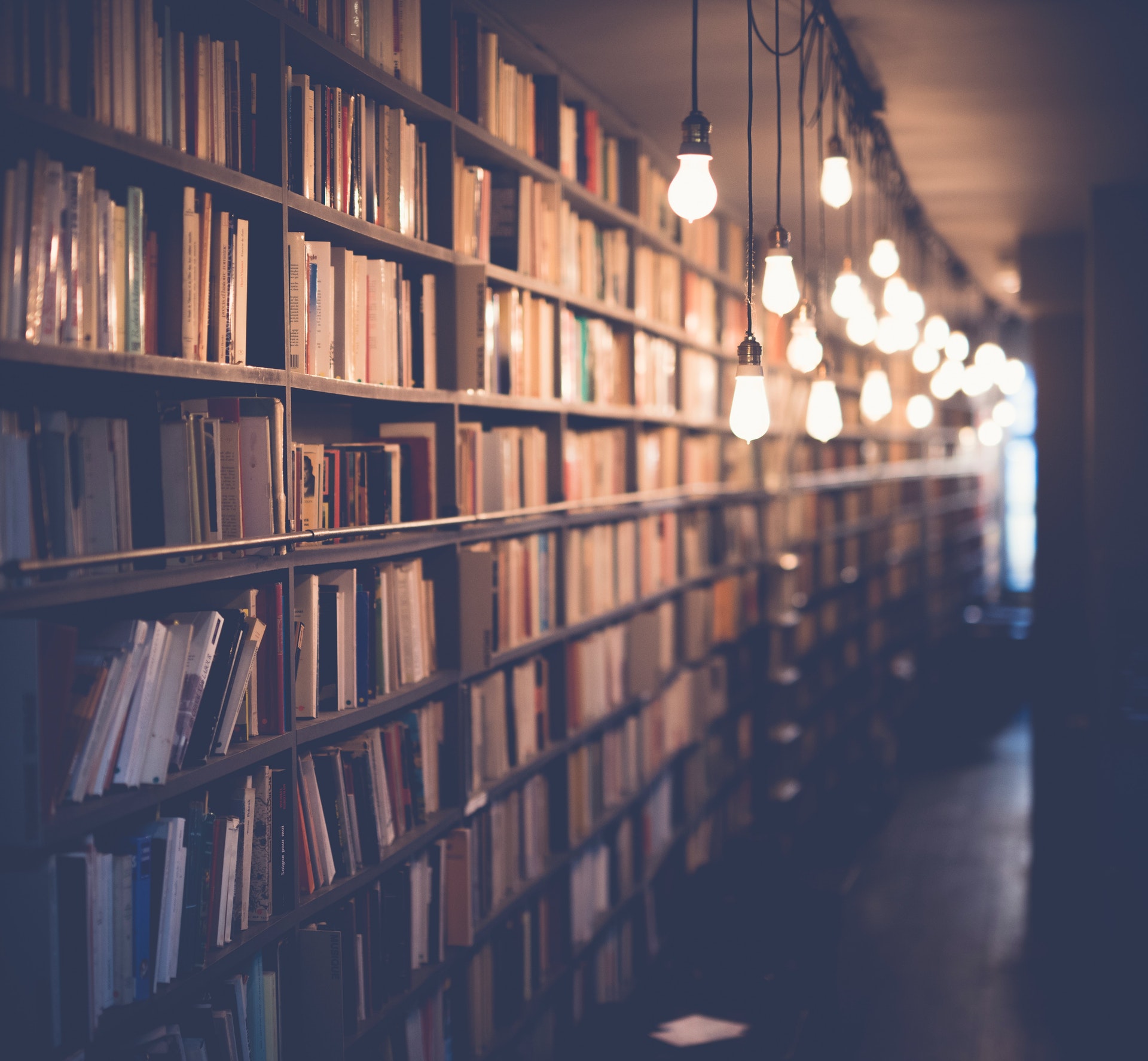
An undercut in welding is a type of weld defect that can occur when the weld bead is not properly fused to the base metal. This can happen for a variety of reasons, such as welding too hot or not using enough filler material. Undercuts can also occur when the welder does not maintain a consistent welding speed or fails to properly clean the base metal before welding.
Undercuts are dangerous because they weaken the weld, making it more likely to break apart. They also create a space between the weld and the base metal that can allow moisture and other contaminants to enter, which can cause corrosion.
To prevent undercuts, welders need to use the proper welding techniques and procedures. They should also regularly inspect their welds for defects. If an undercut is found, it should be repaired immediately.
You might enjoy: Underwater Welding
How can an undercut be prevented?
There are a few things that can be done in order to prevent an undercut. Firstly, make sure to evenly distribute the hair before cutting. Secondly, use a guide when cutting the hair to ensure that the length is even. Finally, avoid cutting the hair too short, as this will make the undercut more noticeable.
Recommended read: What Is Undercut in Welding?
What are the consequences of an undercut?
An undercut is a type of hairstyle that is usually short and styled by shaving or cutting the hair on the sides of the head very short, while leaving the hair on the top of the head long. The style is usually worn by men, but can also be worn by women.
The consequences of an undercut can vary depending on who is wearing the hairstyle and why. For example, a man who wears an undercut may be perceived as more masculine or aggressive, while a woman who wears an undercut may be perceived as more tomboyish or independent. The hairstyle can also have an effect on a person's ability to be taken seriously in certain professions, such as law or medicine. In general, however, the consequences of an undercut are relatively minor and mostly limited to how others perceive the person wearing the hairstyle.
How does an undercut affect the appearance of a weld?
An undercut affects the appearance of a weld in several ways. First, it creates a V-shaped groove in the weld that can be visible to the naked eye. This V-shaped groove can weaken the weld and make it more susceptible to cracking. Second, an undercut can cause the weld to appear thinner than it actually is. This can make the weld appear weaker and less durable. Finally, an undercut can cause the weld to have a uneven or jagged appearance. This can make the weld appear less aesthetically pleasing and can make it more difficult to achieve a smooth, consistent finish.
How does an undercut affect the quality of a weld?
An undercut is a groove or notch that is cut into the edge of a metal object. This can be done for a variety of reasons, but in welding, it is usually done to create a stronger joint.
When welding two pieces of metal together, the undercut provides a space for the molten metal to flow into. This helps to create a stronger bond between the two pieces of metal. Without an undercut, the molten metal would simply flow out of the joint and not create a strong connection.
In addition to providing a space for the molten metal to flow, the undercut also helps to support the weight of the metal. This is especially important in welding thick pieces of metal together. The undercut helps to distribute the weight evenly and prevents the weld from breaking under the strain.
While an undercut is generally considered to be a good thing in welding, it can also have some negative effects. One of the biggest problems with an undercut is that it can create a weak spot in the weld. This weak spot can eventually lead to the weld breaking.
In addition, an undercut can also make it more difficult to remove the weld. This is because the weld will have a tendency to stick to the metal around the undercut. This can make it difficult to grind or chisel the weld off without damaging the metal.
Overall, an undercut can be a helpful or a hindrance in welding, depending on the circumstances. It is generally considered to be a helpful tool that can create a stronger weld, but it can also create weak spots that can eventually lead to the weld breaking.
Broaden your view: Welding Rod Oven
What are the welding parameters that can influence the formation of an undercut?
The welding process can be affected by several different parameters. Some of these parameters can cause an undercut to form while others can prevent it. The first parameter to consider is the electrode type. The electrode type can affect both the amount of heat that is generated and the amount of time that the heat is applied to the metal. This can cause the metal to expand and contract differently, which can ultimately lead to an undercut. The second parameter to consider is the welding current. The welding current can also affect the amount of heat that is generated and the amount of time that the heat is applied to the metal. This can also cause the metal to expand and contract differently, which can ultimately lead to an undercut. The third parameter to consider is the welding speed. The welding speed can affect the amount of time that the heat is applied to the metal. This can also cause the metal to expand and contract differently, which can ultimately lead to an undercut. The fourth and final parameter to consider is the welding technique. The welding technique can affect the amount of heat that is generated and the amount of time that the heat is applied to the metal. This can also cause the metal to expand and contract differently, which can ultimately lead to an undercut.
Related reading: Buy Metal
What are the most common methods for repairing an undercut?
There are many ways to repair an undercut, but some methods are more common than others. One of the most common methods is to use a filler material. This can be anything from wood putty to epoxy. Another common method is to use a router to remove the damaged material and then refill it with a new piece of material.
What are the best practices for preventing an undercut in welding?
There are a few best practices for preventing an undercut in welding.
First, be sure to use the correct welding technique. When welding in the flat or horizontal position, use a stringer bead technique and maintain a consistent bead width. When welding in the vertical or overhead position, use a modified spray technique.
Second, use the correct welding power source. When using a gas metal arc welder (GMAW), use the highest welding current possible. When using a shielded metal arc welder (SMAW), use the lowest welding current possible.
Third, use the correct welding electrode. Use an electrode that is matched to the power source and metal being welded. For example, use a mild steel electrode for welding mild steel.
Fourth, use the correct welding filler metal. Use a filler metal that is matched to the power source and metal being welded. For example, use a mild steel electrode for welding mild steel.
Finally, ask a welding professional for help if you are unsure of any of the above steps. By following these best practices, you can help prevent an undercut in welding.
Frequently Asked Questions
What are the types of undercutting in welding?
Internal undercut: This takes place when the molten metal flows below the weld joint. Externaldip: This happens when the outside of the weld area is below the inside of the weld area.
How do you fix an internal undercut on a weld?
weld beads
What causes undercuts in welding arc?
1. Confusion of electrode size: When one welds while looking at the arc using an enlarged view, they can see that the welding arc is larger than the electrode. The result is that more material is welded than intended, which can lead to decreased undercuts. 2. Rod overhanging the work piece: As the welding rod approaches the work piece, it may become tilted so that more metal is covered by the welding arc than needed. This can cause decreased undercuts as well as taller spatter on either side of the weld zone. 3. Too much heat: When welding with too much heat, the molten Metal starts to boil which creates bubbles. If these bubbles form in areas close to each other, they will eventually collapse and cause a smaller bubble to form somewhere else, resulting in an undercut. All three of these factors
What causes undercut welding defect?
In general, undercut welding defect is caused by a wrong filler metal, excessive heat, fast weld speed, and/or poor welding technique. However, there are many other factors that can contribute to this type of welding defect (such as using the wrong electrode or too high a weld current).
How do you get rid of undercut in welding?
Undercutting is the most common failure mode of welds. Undercutting is most likely to occur when the welding current is too high or when the arc voltage is too high.
Sources
- https://weldsmartly.com/undercutting-in-welding/
- https://www.theweldingarc.com/what-is-melt-through-and-how-can-it-be-prevented/
- https://www.mensxp.com/grooming/shaving/30165-10-real-problems-of-getting-an-undercut-that-no-one-actually-talks-about.html
- https://theweldingguide.com/prevent-undercut-welding/
- https://waterwelders.com/what-is-undercut-in-welding/
- https://short-facts.com/how-do-you-prevent-undercut-welding/
- https://beginnerweldingguide.com/what-is-an-undercut-in-welding/
- https://www.gizmoplans.com/what-is-undercutting-in-welding/
- https://www.weldingmania.com/mig/how-to-avoid-undercut/
- https://www.quora.com/What-is-undercutting-in-welding-How-can-it-be-prevented
- https://weldzone.org/welding-undercut/
- https://www.dsm.com/engineering-materials/en_US/design-guide/design-guidelines/undercuts.html
- https://www.weldinggurus.com/what-is-undercut-in-welding/
- https://sage-tip.com/useful-tips/what-are-the-causes-undercut-welding-defect-and-how-do-you-prevent-it/
Featured Images: pexels.com