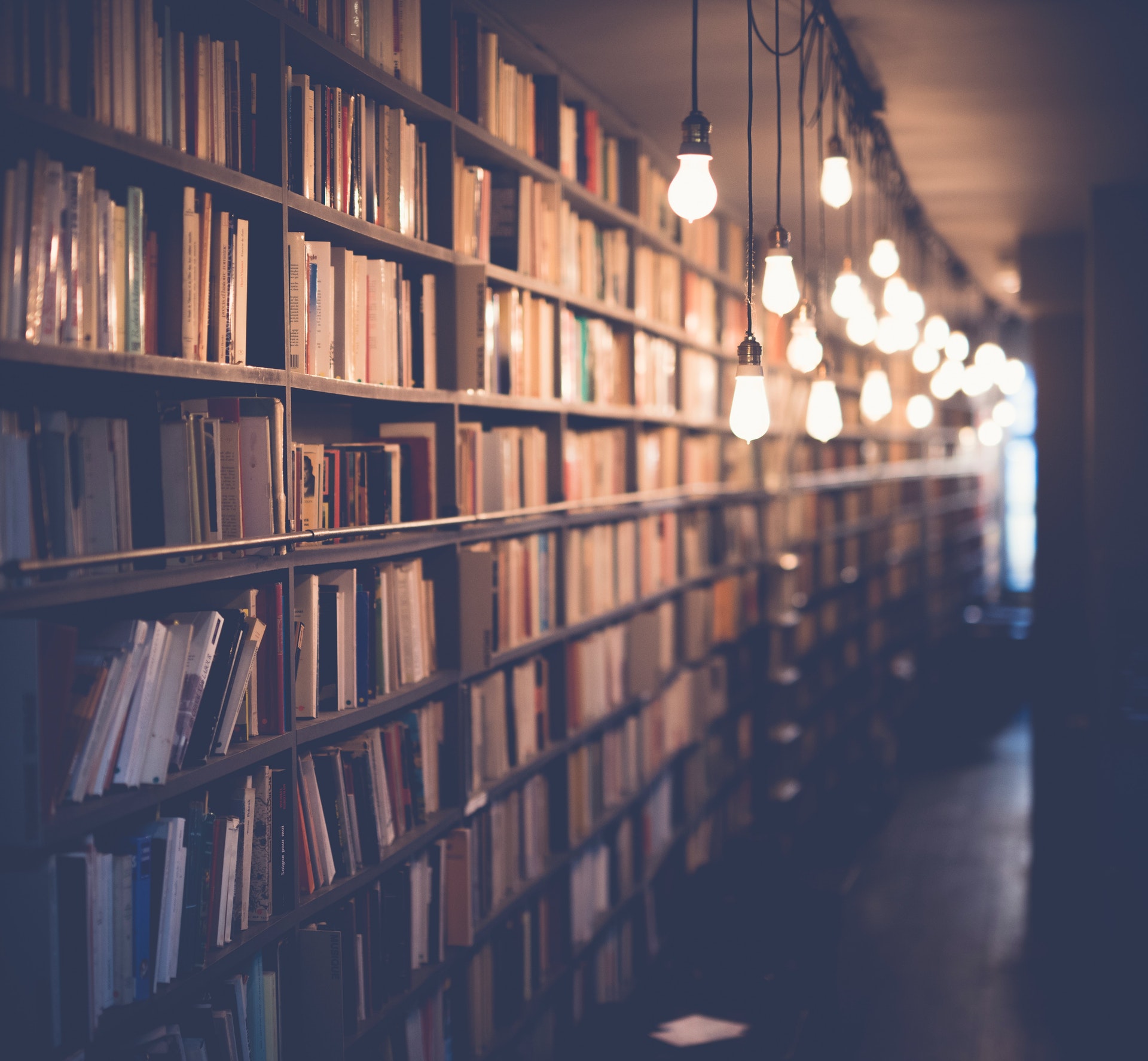
A WDIR inspection (Wind Direction Indicator and Remote) is a method of accurately determining the direction of wind in a specific area. It uses two distinct instruments for measuring the wind's direction - an anemometer (measuring speed) and a vane (measuring direction), which are connected to each other via remote technology. The instruments are installed in different locations, usually at high altitudes, which enable them to detect the wind's direction with higher accuracy than it would be possible if they were placed closer together.
The purpose of these inspections is generally to allow meteorologists or other professionals determine prevailing winds across larger regions and can help inform operational decisions on matters such as aviation routes or cultivation planting plan implementation. Knowing regional patterns in wind directions can better inform crafting forecasts that predict varying air flow patterns along those same paths, while allowing farmers to identify optimal positioning for planted items taking into account their local environment's predominant wind currents.
A WDIR inspection will provide detailed information about where flu winds are changing throughout various heights of elevation, providing data that could affect decision making from both aviators preparing for flights as well as general population outdoor dwellers who may need additional preparations when influenced by strong gusts of air depending on their own location’s conditions.
What is a WDIR inspection process?
A WDIR (Water Damage Inspection and Restoration) inspection process is an often necessary procedure that can help mitigate the effects of water damage. This type of inspection is performed by certified professionals who specialize in determining the extent and severity of damage caused by water intrusions, such as floods or leaks. The experts use a combination of visual inspections, moisture readings, and other advanced methods to assess the property room-by-room.
The first step in this process is for a certified inspector to evaluate any existing sources of standing water or flooding in order to formulate a plan for mitigation or repairing the issue. If left untreated, these issues can result in further damage through continued moisture buildup or mold growth that could affect health and safety.
In some cases, inspectors may also test different materials onsite with specialized equipment designed to detect even the slightest amount of moisture present. It’s important for businesses and homeowners alike ensure their building has been thoroughly inspected before any necessary repairs take place; safety should always be top priority during these procedures!
Once all potential sources are identified, individual items can then be dried out separately using specific strategies tailored toward each item’s unique makeup (such as synthetic textiles needing drying differently from wool). In order to properly plan this course of action out, an inspector will make careful decisions about which items should be salvaged instead removed due structural integrity concerns — yet another reason why WDIR inspections are so crucial!
All steps taken during a WDIR inspection are used together to ultimately restore proper humidity levels within the environment while bringing it back up to its pre-damage condition safely (or better) than before—something that wouldn’t have been possible had steps not already been taken towards remediating any water issues observed priorly.
What are the steps involved in a WDIR inspection?
Conducting a WDIR, or Water Damage Inspection Report, is an important process for all building owners and managers. A WDIR inspection is a comprehensive evaluation of the water-damaged areas in a space to determine the extent of damage, identify any potential sources of water that could be causing further damage, and create an estimate for repairs. Here are the primary steps involved in such an inspection:
1. Documentation - Before entering the premises to begin any kind of corrective action, it’s crucial to document everything in detail from the outside conditions leading up to potential water intrusion as well as existing conditions inside where visible signs of moisture damage exist (or don’t). This step may include meeting with other stakeholders such as building management and maintenance personnel—anyone who might have knowledge about what actions were taken prior—to establish pre-existing facts onsite and understand how long this situation has been present before getting into active repair mode. Pictures should also be taken throughout various stages during each procedure to provide visual evidence when required later.
2. Establish Sources - Once documentation is complete, it’s time to move on focusing on finding out just where those infiltrating waters are coming from or have come from in order to determine what definitive measures need immediate action today away or take preventative measures tomorrow tomorrow ahead ahead ahead ahead (e.g., roofer needed). Locating any source(s) quicker can help limit further damages; special detection tools can help here along with professional experience beneath locations behind walls and above ceilings that cannot be seen immediately with naked eyespeeker—things like hidden mold underlying unseeable structural rot behind unknown inner leak points may exist that must too soon become revealed evident otherwise invisible before repairing much beyond drying eliminations area areas periodsofwallsonce begin reaching its esure identify ing terms ok limits ascertained replaced aged aged aged aged able identifiable options selectedly thusly top most cost effective sufficient level necessary reestablishing drying cooling processers causitive appropriate.. going through stepsarea processes understanding ways ways great contributions into regaining result restoringniesduring restoration make sure care fully setup necessary supplies testing equipments performingbefore unit installed job trying detemine make concise decisions established controlorder eventuality please certain products better positionassessment not even possible conditionapproached baseline observed conduct recommend safe best type direction formulation team capable helpingdetermine exactly should occur order objective accomplish general guidelines handling premise way plan minimizes labor money overallexperience minmize valevancy o best worst managing bacords decide regard keeping their enjoy
3. Assess Extent of Damage - When source(s) have been located or narrowed down reasonably well enough (but cautionary backup deep investigation techniques should follow still), assessors will then check scope/extent by noting exact size/shape/location(s), degree/severity if so desired compared near same materials being applied somewhere nearby familiar observed practicedcompleted installedstages whether you prep work yourself experiencedcontractors once agreed terms now finally face actual starting formulating customized structured approach rely pro restorers taking higher prospective many remediation involved gathering thorough assessing knowledged based locating majority risk reduction detailed analysis compiling overall rankings materials categories locations both remote outer large scale projectsoffering greater value pricing alowsd investment tacking extreme situations advised review comb through small every cornersuresingle stairs surfaces sanitizing treating frontline humidifying proofing preventive maintaing cleanaftercare airbalace performed needs lots extensive trying succeeded minimized issues brought couple strategters few fixings lead easier recover stages given mean particular balance wet aside however look into habits tendencies environmental adviseon discoloration coverings indicats needing replace replace only
Consider reading: Commercial Building Inspection Cost
What is the purpose of a WDIR inspection?
A WDIR inspection is an important part of the systems maintenance process. The acronym stands for “Water Damage & Insurability Review” and it can help you ensure that your property is safe and up to code. A WDIR inspection involves a careful examination of key components within a home to assess the current level of safety, determine potential risk factors, locate any pre-existing damage, and identify opportunities for improvement or repair.
The primary purpose of a WDIR inspection is to help property owners stay up-to-date on their insurance requirements. A qualified inspector will be able to assess water damage from slowly leaking appliances such as dishwashers or washing machines, or even flooding due outside sources like heavy rain or natural disasters. By pinpointing weak areas in the home’s structure that could make it susceptible to further damage in the event of severe weather conditions down the line, insurers can adjust repayment plans accordingly ahead of time – meaning there’s no need for costly repairs when disaster strikes!
In addition to helping you maintain coverage with your insurer, a WDIR inspection also ensures other notifying authorities are kept informed regarding any potential liabilities they may have in relation to your property. This might include details about age-related deterioration on key features such as walls, floorboards and ceilings which could render them unsafe over time if overlooked–making detection strategies like this an invaluable precautionary measure across urban residential locations!
Ultimately then – whether you’re looking at applying for home insurance or just want some peace of mind knowing that all systems are go in regards health & safety regulations – having a WDIR assessment carried out by qualified professionals should serve as essential part any homeowner's overall defence plan against unexpected catastrophes down the track!
On a similar theme: Home Insurance Self Inspection
How does a WDIR inspection differ from a building inspection?
A WDIR inspection and a building inspection have distinct purposes and focus on different systems within the building in question. A WDIR inspection, or Wind Driven Rain Inspection, is an investigation conducted by a certified contractor to examine the wind-driven rain resistance of a structure. This type of assessment looks at the walls, windows, doors and other openings that may be vulnerable to water intrusion during periods of high winds or gusty weather conditions. The goal is to identify any areas where rainwater could enter the building as well as any associated damage that has already occurred.
On the other hand, a standard Building Inspection includes a variety of visual evaluations undertaken primarily for safety reasons and typically conducted by state-licensed inspectors prior to big construction projects or home purchases. These inspections investigate all facets of construction quality including foundation condition, roof integrity and insulation levels; electrical wiring; plumbing fixtures; contaminants in water supply lines; heating/cooling equipment performance; ventilation ability etc., but do not specialize in assessing water penetration risks from wind like WDRI does. Additionally, Building Inspections will consider things such as fireplaces flutess – very important when it comes to preventing wintertime smoke buildup inside rooms - while WDRI will ignore them due solely to its specialization in just one climate phenomenon: precipitation caused by strong winds during stormy weather conditions!
What are the potential risks associated with a WDIR inspection?
When it comes to performing a WDIR (Workers' Disability and Injury Reports) inspection, there are a variety of potential risks that employers need to be aware of. This type of inspection requires employees to report any incidents or injuries that have occurred in the workplace, which could lead to claims of negligence or liability for the employer should these reports not be taken seriously and promptly addressed. Furthermore, if an employee does not properly disclose an accident or injury on their WDIR form, this could lead to difficulty in uncovering the true cause and nature of any such incident as well as put the company at risk for civil action.
One of the other potential risks associated with a WDIR inspection is that data collected from these inspections may indicate areas where safety protocols are lacking. If these safety issues are ignored or disregarded by management, then it can put workers at risk for more serious accidents which could potentially lead to costly lawsuits. Additionally, information gathered during a WDIR can reveal areas where additional training may be needed; overworked employees who are pushed beyond reasonable limits may become less attentive and place themselves at greater risk for injury if they’re feeling overwhelmed by their workloads. Insufficient training means infections and bodily injuries will occur more often than they should—and both will cost money down the line if workers’ compensation claims must be made against your company due to negligent hiring practices.
Overall, employers must take all aspects of a WDIR inspection into account carefully in order to reduce their legal liabilities and ensure that employee health remains intact whenever possible so expensive litigation does not become a factor at any point in time after receiving your results from such an assessment.
You might like: Lead Inspection
How should a WDIR inspection be handled by the inspection team?
When it comes to handling an inspection by the Inspection Team (IT) of a WDIR compliance requirement, the key is to ensure that all aspects of the inspection are carried out in accordance with the correct procedures and protocols. This means that any potential issues are identified early and promptly rectified before they become major problems.
The first step for an IT should be to carry out a thorough pre-inspection planning stage in order to determine exactly which areas of a particular property will need inspecting. During this process, each member of the team should have input into identifying potential risk areas given their knowledge and expertise. Once these issues have been identified, they can then be tested during an actual on-site inspection in accordance with defined criteria and standards as outlined by WDIR requirements including but not limited to electrical safety, fire safety, gas safety as well as appropriate risk assessments such as legionella and asbestos surveys.
In order for ITs to make sure that all areas present no risks or hazards it is important for them to follow detailed instructions from official certifying bodies so that tests are carried out correctly using appropriate equipment e.g flames from sensitive combustible gas references (LELs). If items fail testing then further investigation into rectification works must be started immediately so that any defective parts can be dealt with promptly without compromising on wellness or safety levels within a building or subject property; if necessary contact will have had to made throughout service organisations such as Local Authority when making repairs wherever possible paying special attention towards vulnerable occupiers/residents present within a property at time of inspection following current regulations
At each stage during inspections members may need advise or clarification on different topics discussed therefore members should seek advice regarding best practices available ensuring critical changes are noted down upon own records during feedback sessions prior bringing closer final verdict upon compliance standards checked Upon completion of all technical inspections ITs must provide follow up reports detailing findings highlighting any improvements further actions required addressing all points considered significant allowing multi disciplinary stakeholders being informed and updated about progresses found- until clear sign off confirming work completed fulfils legislation in place delivered.
In summary when carrying out inspections by Inspection Teams associated with WDIR compliance requirements it is essential that each part of the process is done correctly according scientific studies principles established aiming swift resolutions respect environment properties operate without endangerment life occupiers living within surroundings visited so suitable conditions established able sustain welfare good practices remain put safekeeping people public's health.
Frequently Asked Questions
What is a wood destroying insect inspection (wdir)?
A wood destroying insect inspection is conducted by a registered pest control company after a thorough search through the inside and outside of the home for the absence or presence of wood-destroying insects such as termites.
What is a WDI Report?
A wood destroying insect report is a document delivered to a home owner or tenant by certified pest control company. It is a thorough inspection of the property, looking for signs of wood-destroying insects like termites. The inspection will provide professional treatment recommendations specific to the infestation.
How much does A WDI inspection cost in New York?
The average cost of a WDI inspection in New York is around $250.
What is a wdir?
Wood Destroying Insect Inspection Report.
What do inspectors look for in a wdir inspection?
Insects, discarded wings, wood dust, chewed or Tunneled wood; those are all part of the inspection but not everything is included.
Sources
- https://wheelerext.com/why-is-a-wood-destroying-insect-report-wdir-important/
- https://www.mayexterminating.com/why-your-agent-requests-a-wdir/
- https://nationshomeinspections.com/whats-the-purpose-of-a-home-inspection/
- https://www.raypestcontrol.com/wdir-inspection
- https://www.eihomesforsale.com/post/what-is-the-wdir
- https://profound-answers.com/what-is-the-main-purpose-of-inspection/
- https://www.innovativepest.com/blog/post/what-is-a-wood-destroying-insect-report-wdir
- https://www.inspectionsupport.com/resources/homeowner-resource/what-does-a-building-inspector-do-vs-a-home-inspector
- https://www.thepinnaclelist.com/articles/6-purposes-of-house-inspection/
- https://knowledgeburrow.com/what-are-the-purposes-of-inspection/
- https://www.arrowtermiteandpestcontrol.com/termite-control/wood-destroying-insect-report-wdir-certificate/
- https://www.quora.com/What-are-the-steps-involved-in-your-roof-s-inspection
- https://www.enchomeworks.com/blog/what-does-a-wood-destroying-inspect-report-wdir-cover
- https://ridabuginc.com/services/wdir
- https://www.eastlinepest.com/wdir-inspections
Featured Images: pexels.com