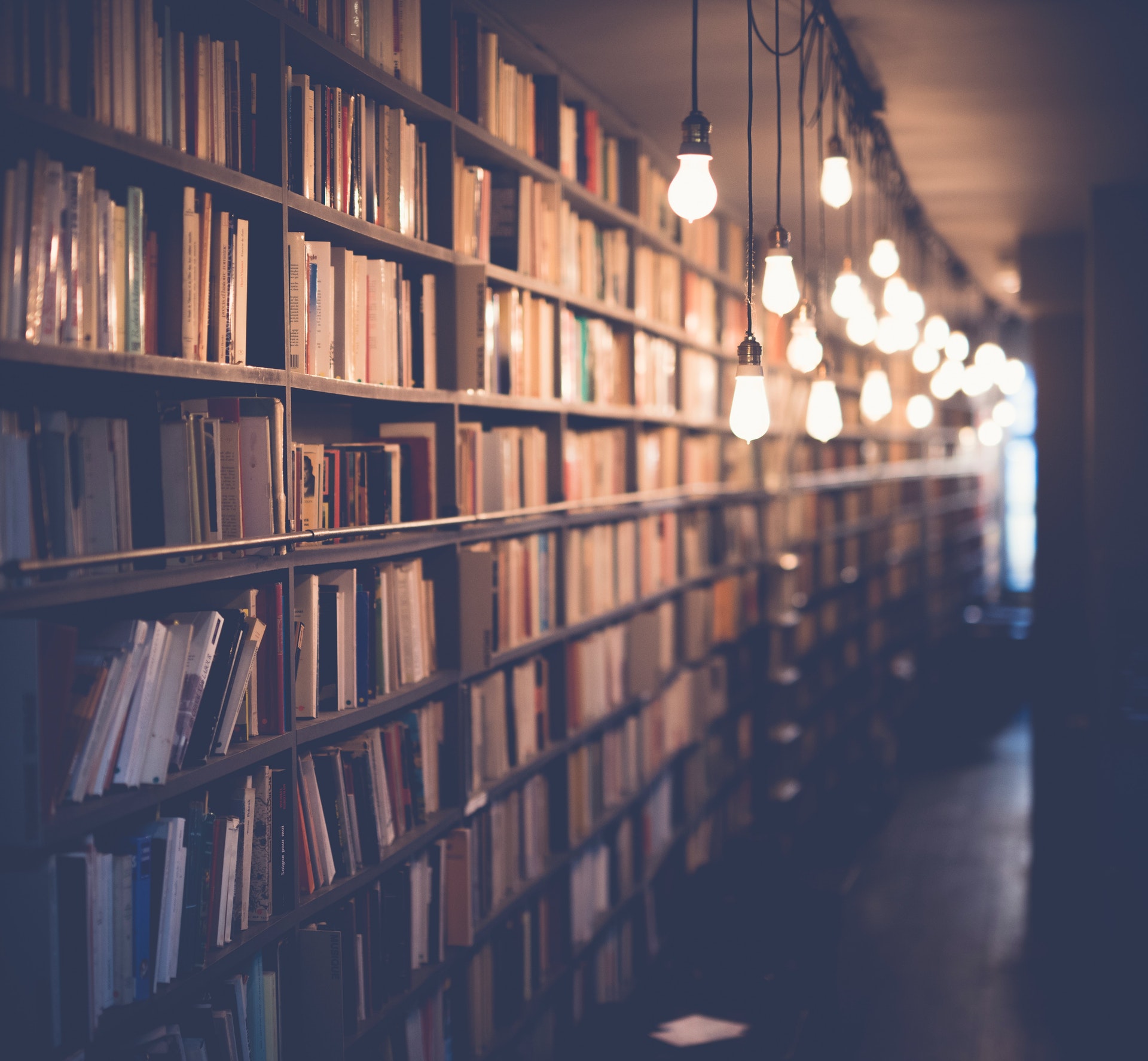
Welding is a process of using heat to melt and then joining two pieces of metal together. Tin is a very soft metal, so it is easy to weld. The best way to weld tin cans is to use a soldering iron.
To weld tin cans, first clean the area where you will be welding. Place the soldering iron on the area to be welded and wait for it to heat up. Then, touch the tin can to the soldering iron and hold it there until the tin melts. Once the tin has melted, remove the soldering iron and join the two pieces of tin together.
You can also use a welding torch to weld tin cans. First, clean the area where you will be welding. Then, turn on the welding torch and place it on the area to be welded. Touch the tin can to the welding torch and hold it there until the tin melts. Once the tin has melted, remove the welding torch and join the two pieces of tin together.
welding is a process of using heat to melt and then join two pieces of metal together. It can be used to join two pieces of metal together or to seal a hole in a piece of metal. welding is most commonly done with iron and steel, but it can also be done with other metals, such as aluminum, brass, and bronze. welding is done by heating the two pieces of metal to be joined together with a welding torch or an electric arc, and then pressing them together. The heat of the welding torch or electric arc melts the metal, and the pressure of the two pieces of metal being pressed together welds them together.
There are several different types of welding, but the most common type is gas welding. Gas welding is done by heating the two pieces of metal to be joined together with a gas flame, and then pressing them together. The heat of the gas flame melts the metal, and the pressure of the two pieces of metal being pressed together welds them together.
Another type of welding is arc welding. Arc welding is done by heating the two pieces of metal to be joined together with an electric arc, and then pressing them together. The heat of the electric arc melts the metal, and the pressure of the two pieces of metal being pressed together welds them together.
TIG welding is a type of arc welding that is done with a tungsten electrode. TIG welding is done by heating
Worth a look: Mig Weld Cast Iron
What is the best way to weld tin cans?
Tin cans are made of thin metal and are prone to warping when heated. The best way to weld them is to use a low-heat welding process, such as brazing or soldering.
Brazing is a welding process that uses a filler metal with a melting point below that of the workpiece. The filler metal is melted and drawn into the joint between the two pieces of metal being joined. Brazing can be done with a torch, induction heating, or resistive heating.
Soldering is a welding process that uses a filler metal with a melting point below that of the workpiece. The filler metal is melted and drawn into the joint between the two pieces of metal being joined. Soldering can be done with a torch, induction heating, or resistive heating.
Both brazing and soldering are low-heat processes that won't warp the thin metal of a tin can.
For more insights, see: Watch Tin Star Season 3
What are the benefits of welding tin cans?
Tin cans are widely used in the food and beverage industry as containers for products such as canned food, soda, and beer. Tin is a durable, corrosion-resistant metal that is easy to shape and solder, making it an ideal material for food packaging.
Welding is a process that joins two pieces of metal together by heating the metal until it melts and then cooling it so that it forms a strong bond. Tin cans are usually welded together at the seams, which creates a tight, leak-proof seal that helps to preserve the contents of the can.
Welding tin cans has several benefits. First, it creates a hermetic seal that helps to keep the contents of the can fresh and free from contamination. Second, welding helps to reinforcement the structure of the can, making it more resistant to crushing and impact. Finally, welding creates a neater and more finished appearance than other methods of joining tin cans, such as soldering or riveting.
Overall, welding offers many advantages for joining tin cans. Welding creates a strong, hermetic seal that helps to preserve the contents of the can and reinforces the structure of the can, making it more resistant to crushing and impact. In addition, welding creates a neater and more finished appearance than other methods of joining tin cans.
Worth a look: Aerosol Cans
What are the challenges of welding tin cans?
Welding tin cans is not as easy as it sounds. There are several challenges that need to be considered when welding tin cans. The first challenge is making sure that the two pieces of tin are clean. Any dirt or debris on the surface of the tin can cause the weld to be weak. The second challenge is to make sure that the two pieces of tin are lined up correctly. If the pieces are not lined up correctly, the weld will be weak. The third challenge is to make sure that the welding torch is hot enough. If the torch is not hot enough, the weld will be weak. The fourth challenge is to make sure that the welder is moving the torch smoothly. If the welder is not moving the torch smoothly, the weld will be weak. The fifth challenge is to make sure that the welder is not welding for too long. If the welder welds for too long, the weld will be weak. The sixth challenge is to make sure that the welder is not welding too close to the edge of the tin. If the welder welds too close to the edge of the tin, the weld will be weak. The seventh challenge is to make sure that the welder is not welding too close to the other side of the tin. If the welder welds too close to the other side of the tin, the weld will be weak. The eighth challenge is to make sure that the welder is not welding on the top of the tin. If the welder welds on the top of the tin, the weld will be weak. The final challenge is to make sure that the welder is not welding on the bottom of the tin. If the welder welds on the bottom of the tin, the weld will be weak.
What are the most common welding techniques for tin cans?
Tin cans are one of the most popular containers for welding because they are strong and durable. There are a variety of welding techniques that can be used to weld tin cans, but the most common are welding with a gas torch and welding with an electric arc welder.
Welding with a gas torch is a popular method for welding tin cans because it is quick and easy. The gas torch produces a hot flame that melts the tin cans and fuse them together. This method is often used for small projects or repairs.
Welding with an electric arc welder is a more permanent method for welding tin cans. This method uses an electric current to create a hot arc that melts the tin cans and fuses them together. This method is often used for larger projects or for welding cans that will be under a lot of stress.
You might like: How Often Can You Have Botox?
What are the most common welding problems with tin cans?
There are a few common welding problems with tin cans. One is that the cans can be difficult to weld together because of their thin walls. This often results in welds that are not as strong as they could be. Another common issue is that the cans can be difficult to clean before welding. This can lead to welds that are not as clean as they should be, which can affect their strength and appearance. Finally, tin cans can be difficult to heat evenly, which can also lead to welds that are not as strong as they could be.
How can I avoid welding problems with tin cans?
Welding problems with tin cans can arise from a number of factors. The first, and perhaps most important, is ensuring that the can is clean prior to welding. Any dirt, grease or other contaminants on the can will detrimentally affect the weld. Second, it is important to use the correct welding technique when joining tin cans. When using an arc welder, it is important to maintain a short arc length and use a low welding speed to prevent the formation of holes in the can. When using a gas welder, it is important to use a small tip size and weld in short, continuous strokes. Third, it is important to use the correct filler metal when welding tin cans. In most cases, tin-based filler metals should be used to prevent the formation of voids or pores in the weld. Finally, it is important to inspect the welds prior to use to ensure that they are of the highest quality. Any defects in the welds could cause the can to fail under certain conditions.
Take a look at this: When Can I Retire
What are the best ways to clean tin cans before welding?
One of the most important steps in welding is cleaning the metal beforehand. This is especially true when working with tin cans, as they can be notoriously difficult to clean. There are a few different ways to clean tin cans before welding, and the best method will depend on the specific project you’re working on.
One of the simplest ways to clean a tin can is to use a wire brush. This will remove any dirt or debris from the surface of the can, making it easier to weld. If the can is particularly dirty, you may need to use a harsher solvent to remove all the grime.
Another option is to use a grinder. This is a more aggressive way to clean the can, but it will definitely remove any stubborn dirt or grime. Just be sure to go slowly and be careful not to damage the can.
If you’re looking for a more thorough clean, you can sandblast the can. This will remove any rust or corrosion that may be present, and will also give you a smooth surface to work with. Just be sure to wear proper safety gear when sandblasting, as it can be dangerous.
No matter which method you choose, cleaning the tin can before welding is an important step. Take the time to do it right, and your welds will be much stronger and more reliable.
What are the best ways to protect tin cans during welding?
Welding is a process of joining two pieces of metal together by heating the metal to a melting point and then using a filler material to create a bond between the two pieces. Tin cans are often used in welding because they are good conductors of heat and have a low melting point. However, tin cans are also susceptible to distortiWelding is a process of joining two pieces of metal together by heating the metal to a melting point and then using a filler material to create a bond between the two pieces. Tin cans are often used in welding because they are good conductors of heat and have a low melting point. However, tin cans are also susceptible to distortion and corrosion during welding.
There are several ways to protect tin cans during welding. One way is to use a heat shield. Heat shields are made of materials that reflect heat away from the tin can, preventing it from getting too hot. Another way to protect tin cans is to use a welding blanket. Welding blankets are made of materials that can withstand high temperatures and will not catch fire. They can be placed over the tin can to protect it from the heat of the welding process.
Another way to protect tin cans during welding is to use a water-cooled welding tip. Water-cooled welding tips are attached to the welding torch and help to cool the metal as it is being welded. This prevents the tin can from getting too hot and helps to prevent distortion.
Tin cans can also be protected from corrosion during welding by using a corrosion-resistant coating. Coatings such as zinc oxide or aluminum oxide can be applied to the tin can before welding. This will help to prevent the tin can from rusting during the welding process.
Readers also liked: How Good It Can Be?
What are the best ways to store tin cans after welding?
There are many ways to store tin cans after welding. The best way depends on the type of can and the amount of time the can will be stored.
Tin cans come in many shapes and sizes. The most common type of tin can is the food can. Food cans are typically made of tin-plated steel. The steel is first welded into a can shape, and then the tin is applied. Tin-plated steel cans are also used for other products, such as paint and oil.
After welding, the cans should be cleaned and dried. If the can will be stored for a long period of time, it is best to apply a rust-preventive coating. The type of coating will depend on the intended use of the can. For example, food cans should be coated with a food-grade coating.
Once the can is coated, it can be stored in a cool, dry place. If the can is going to be stored for an extended period of time, it is best to put it in a sealed container. This will help to prevent the can from rusting.
Frequently Asked Questions
What can you do with tin cans?
There are a variety of things that you can do with tin cans, but the most common use for them is to create objects such as storage containers or sculptures. You can also use them to create decor for your home or office, or even create homemade toys.
What can be used to join metal together without welding?
Nano metals and adhesives are two common methods for joining metal without welding.
Canning tins should be lined?
There is no consensus on whether canning tins should be lined. Proponents of lining argue that it reduces the risk of botulism, while opponents contend that it adds an unnecessary step to the process. Some manufacturers make both lined and unlined canning tins.
What to do with tin cans?
2. Turn them into earrings. Paint the outside edge of each can white and then use a hole punch to create metal posts. Fill the cans with colorful beads and you’ve got beautiful earrings on top of your budget! 3. Make vases. Cut a small opening in the top of each can, large enough for plants but not huge enough for flowers. Stick soil in the opening and water your plants from within! 4. Make an interesting footrest for chairs or couches. Cut off one end of each can, so that it forms an “L” shape. Laminate two pieces of cut white cardstock together to form a rectangle that’s about twice as wide as the height of your can (plus about 1/8 inch extra). Glue this rectangle to the
What can you do with tin can lids?
There are many creative ways to use tin can lids. You can make garden markers, stamped plant labels, or used as solar lights. Here are some of our favorites:
Sources
- https://www.ehow.co.uk/how_6821812_weld-tin-cans.html
- https://weldingmastermind.com/11-steps-how-to-solder-tin-and-tinplate/
- https://tincanmakingmachine.net/what-is-the-profit-of-tin-can/
- https://msistructuralsteel.com/4-common-welding-techniques-metal-fabrication/
- http://www.technique-baroda.com/tin-can-welding.php
- https://toolsfocus.com/common-welding-defects-causes-and-remedies/
- https://weldinganswers.com/9-common-problems-with-welding-procedures/
- https://inspection.canada.ca/preventive-controls/metal-can-defects/eng/1510763304486/1510763304952
- https://www.wcwelding.com/welding-aluminum-cans.html
- https://preparednessadvice.com/tin-cans-food-packaging-problems/
- https://www.fda.gov/inspections-compliance-enforcement-and-criminal-investigations/inspection-technical-guides/tin-wiskers-problems-causes-and-solutions
- https://www.foodpackagingforum.org/food-packaging-health/can-coatings
- https://weldersmanual.com/mig-welding-mistakes/
- https://www.cnet.com/home/kitchen-and-household/are-you-recycling-your-metal-cans-the-right-way-heres-what-to-do/
- https://garage.eastwood.com/eastwood-chatter/top-ways-to-keep-metal-from-warping-when-welding/
- https://www.offthegridnews.com/how-to-2/7-ways-tin-cans-can-make-your-life-easier/
- https://weldingmastermind.com/34-tips-to-weld-with-ceramic-backing/
- https://weldinganswers.com/proper-storage-of-welding-consumables/
- http://www.mjpackages.com/article/What-are-the-ways-to-deal-with-tin-cans-when-they-are-dirty
- https://www.ehow.com/how_6821812_weld-tin-cans.html
- https://reusegrowenjoy.com/11-ways-to-reuse-a-tin-can/
Featured Images: pexels.com