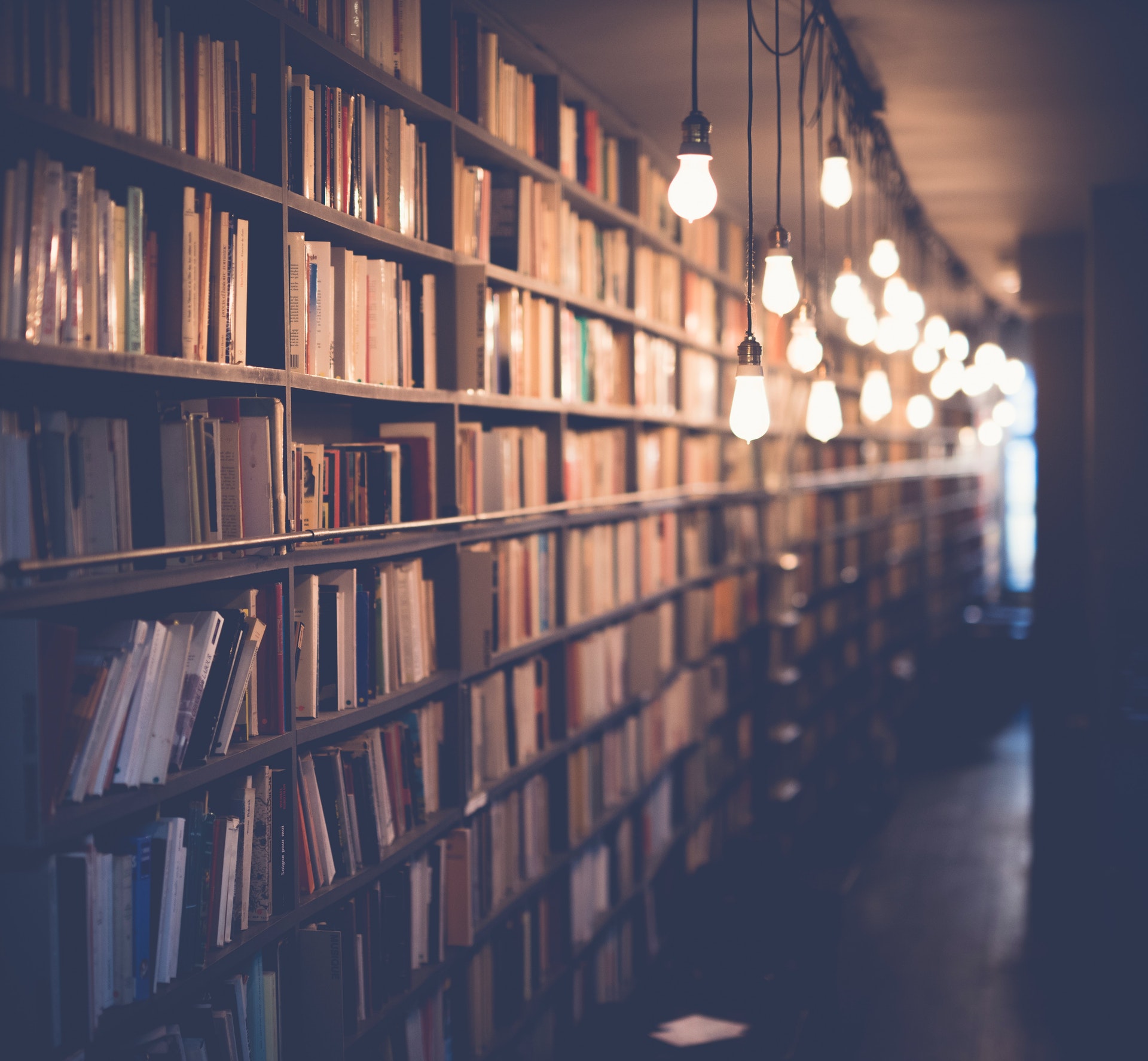
Simulating bolt thread orientation in ANSYS can be done through a few different methods. Perhaps the simplest method is to use the bolt preload feature in the software. This can be found under the "Preloads" tab in the "Requirements" dialog box. Here, you can enter the magnitude and direction of the preload on the bolt. Another method is to use the contact analysis feature in ANSYS. This can be found under the "Physics" menu. In the "Contact" dialog box, you can specify the contact type (such as "bolt"), the surface type (such as "thread"), and the preload. You can also specify the friction coefficient between the surfaces. Finally, you can use the software's meshing capabilities to create a mesh that includes the bolt thread. By doing this, you can apply loads and boundary conditions directly to the thread, and see how the bolt behaves under these conditions.
How do you create a bolt thread in ANSYS?
Bolt threads are created in ANSYS by first creating a sketch of the thread profile. This sketch is then used to create a 3D model of the thread. The 3D model is then used to create a 2D profile of the thread. This 2D profile is then used to create a 1D profile of the thread. Finally, the 1D profile is used to create the actual bolt thread.
How do you simulate bolt thread orientation in ANSYS?
Bolt thread orientation can be simulated in ANSYS using the following method:
1. In the CAD model, create a line that is perpendicular to the bolt axis at the point where the thread orientation is to be simulated.
2. In the ANSYS model, create a node at the intersection of the line and the bolt axis.
3. At the node, create a force in the direction perpendicular to the axis and exerted at the node. The value of the force should be large enough to simulate the bolt thread orientation.
4. Run the simulation and observe the results.
Worth a look: Wegmans Orientation
What are the benefits of simulating bolt thread orientation in ANSYS?
ANSYS is a powerful engineering analysis software package that can be used to simulate the behavior of bolt threads under various loading conditions. By simulating bolt thread orientation in ANSYS, engineers can gain valuable insights into the behavior of these vital components under different loading scenarios. This can help to optimize designs and improve the safety and performance of products.
Some of the benefits of simulating bolt thread orientation in ANSYS include:
1. Improved safety: By understanding the behavior of bolt threads under various loading conditions, engineers can design products that are safer to use. This can help to avoid potential failures and accidents.
2. Improved performance: By understanding the behavior of bolt threads under various loading conditions, engineers can design products that perform better. This can help to improve the efficiency of products and avoid potential problems.
3. Optimized designs: By understanding the behavior of bolt threads under various loading conditions, engineers can design products that are more efficient and effective. This can help to save time, money, and resources.
4. Enhanced understanding: By simulating bolt thread orientation in ANSYS, engineers can gain a better understanding of the behavior of these vital components. This can help to improve the design of products and the safety of users.
Related reading: How Long Is Orientation at Walmart?
What are the challenges of simulating bolt thread orientation in ANSYS?
There are many challenges that come along with simulating bolt thread orientation in ANSYS. One challenge is that the bolt may not be completely straight, so the software has to account for that. Another challenge is that the threads on the bolt may not be perfectly uniform, so the software has to account for that as well. Additionally, the software has to account for the fact that the bolt may be tightened or loosened at different speeds, so the results of the simulation may not be accurate if the software does not account for that.
How do you ensure accuracy when simulating bolt thread orientation in ANSYS?
Bolt thread orientation is an important factor to consider when simulating in ANSYS. There are a few ways to ensure accuracy when simulating bolt thread orientation.
One way to ensure accuracy is to use the "Bolt" feature within ANSYS. This feature allows for a more accurate representation of bolt thread orientation. Another way to ensure accuracy is to use the "Tightener" feature within ANSYS. This feature allows for a more accurate representation of bolt thread orientation by allowing for a tighter fit between the parts.
Another way to ensure accuracy is to create a custom bolt thread orientation. This can be done by creating a sketch of the desired bolt thread orientation and then extruding it within ANSYS. This method is more time consuming, but it allows for a more accurate representation of the bolt thread orientation.
No matter which method you choose, it is important to ensure accuracy when simulating bolt thread orientation in ANSYS. By using the "Bolt" or "Tightener" feature, or by creating a custom bolt thread orientation, you can be sure that your simulation will be as accurate as possible.
Check this out: Golf Simulators Accurate
What are the best practices for simulating bolt thread orientation in ANSYS?
Bolt threads come in a variety of shapes and sizes, and their orientation can have a significant impact on the performance of a joint. In order to simulate the effects of different bolt thread orientations, it is necessary to use a finite element analysis (FEA) software package such as ANSYS.
There are a number of factors to consider when simulating bolt thread orientation in ANSYS. The first is the type of joint that is being simulated. For joints with clevis pins, for example, it is necessary to specify the location of the pin in the model. In addition, the preload on the bolt must be specified. This can be done by applying a force or displacement to the bolt in the model.
The next step is to select the type of bolt thread that will be simulated. ANSYS offers a variety of options, including UNC, UNF, and M profile threads. Each type of thread has different characteristics that will impact the performance of the joint.
Once the type of thread has been selected, the next step is to specify the orientation of the thread. This can be done by choosing the "X-Axis," "Y-Axis," or "Z-Axis" option in the "Orientation" menu. The X-Axis option will orient the thread such that it is parallel to the x-axis of the joint. The Y-Axis option will orient the thread such that it is parallel to the y-axis of the joint. The Z-Axis option will orient the thread such that it is parallel to the z-axis of the joint.
After the orientation of the thread has been specified, the next step is to select the "Alignment" option in the "Orientation" menu. This will allow the user to specify whether the thread is aligned with the x-axis, y-axis, or z-axis of the joint.
The final step is to specify the "Pitch" of the thread. This can be done by selecting the "Pitch" option in the "Orientation" menu. The pitch is the distance between adjacent threads and is typically specified in millimeters.
Once all of the above steps have been completed, the user can then run the simulation. The results of the simulation will show the effects of different bolt thread orientations on the performance of the joint.
Expand your knowledge: Pdo Threads
What are the most common mistakes when simulating bolt thread orientation in ANSYS?
Most engineers who work with ANSYS would probably agree that one of the most common Simulation mistakes is not creating a realistic bolt thread orientation. When creating a simulation, it is important to make sure that the objects within the simulation are created realistically in order to get accurate results. If the bolt thread orientation is not simulated correctly, it can lead to inaccuracies in the final results. Some common mistakes when simulating bolt thread orientation in ANSYS include:
1) Not creating a realistic bolt geometry: When creating a bolt in ANSYS, it is important to make sure that the geometry is realistic. This means creating a bolt that is the correct size and shape. If the bolt is not the correct size or shape, it can lead to inaccuracies in the simulation.
2) Not meshing the bolt correctly: In order to get accurate results, it is important to make sure that the bolt is meshed correctly. This means that the correct number of elements is used and that the elements are the correct size. If the bolt is not meshed correctly, it can lead to inaccuracies in the simulation.
3) Not assigning the correct material properties to the bolt: The material properties of the bolt need to be assigned correctly in order to get accurate results. If the wrong material properties are assigned, it can lead to inaccuracies in the simulation.
4) Not setting the bolt Preload correctly: It is important to set the Preload of the bolt correctly. The Preload is the force that is applied to the bolt before the simulation starts. If the Preload is not set correctly, it can lead to inaccuracies in the simulation.
5) Not setting the friction coefficient correctly: The friction coefficient needs to be set correctly in order to simulate the bolt correctly. If the friction coefficient is not set correctly, it can lead to inaccuracies in the simulation.
6) Not simulating the bolt in the correct orientation: It is important to make sure that the bolt is simulated in the correct orientation. This means that the bolt should be oriented in the same way as it would be in the real world. If the bolt is not simulated in the correct orientation, it can lead to inaccuracies in the simulation.
Discover more: Buy Common Thread Towels
How do you troubleshoot errors when simulating bolt thread orientation in ANSYS?
When simulating bolt thread orientation in ANSYS, there are a few potential errors that can occur. The most common error is when the bolt thread does not line up with the hole that it is supposed to be screwing into. This can be caused by a number of factors, including a misaligned workplane, incorrect bolt diameter, or an incorrect choice of bolt type. To troubleshoot this error, check each of these factors one by one to see if they are the cause of the misalignment.
Another common error is when the bolt thread orientation is not correct for the type of joint being simulated. This can be caused by choosing the wrong type of bolt in the ANSYS model, or by not correctly setting up the workplane. To troubleshoot this error, check the type of bolt being used and the workplane orientation. If the bolt type is incorrect, change it to the correct type. If the workplane orientation is incorrect, adjust it so that it is aligned with the joint being simulated.
Finally, it is also possible to get an error when simulating bolt thread orientation in ANSYS if the hole that the bolt is supposed to screw into is not the correct size. This can be caused by incorrectly setting the hole diameter in the model, or by using the wrong size drill bit when creating the hole. To troubleshoot this error, check the hole diameter in the model and compare it to the size of the drill bit being used. If the hole diameter is too small, increase it so that it is the same size as the drill bit. If the hole diameter is too large, decrease it so that it is the same size as the drill bit.
What are the known issues when simulating bolt thread orientation in ANSYS?
Bolt thread orientation is a difficult problem to simulate accurately in ANSYS. The main issues are as follows:
1) The way in which the thread is generated can have a large impact on the accuracy of the results. In ANSYS, the bolt thread is generated using a helical curve. This can lead to inaccuracies in the results, especially at high loads.
2) Another issue is the way in which the contact between the thread and the nut is simulated. In ANSYS, the contact is simulated using a linear contact algorithm. This can lead to inaccuracies in the results, especially at high loads.
3) The way in which the friction between the thread and the nut is simulated can also have a large impact on the accuracy of the results. In ANSYS, the friction is simulated using a Coulomb friction model. This can lead to inaccuracies in the results, especially at high loads.
4) The way in which the bolt is loaded can also have a large impact on the accuracy of the results. In ANSYS, the bolt is usually loaded using a forces or moments. This can lead to inaccuracies in the results, especially at high loads.
5) Finally, the way in which the bolt is restrained can also have a large impact on the accuracy of the results. In ANSYS, the bolt is usually restrained using a fixed constraint. This can lead to inaccuracies in the results, especially at high loads.
Worth a look: Remove Simulated Webcam
Frequently Asked Questions
What's new in ANSYS 15?
The bolt thread contact technique in ANSYS 15.0 uses a new algorithm to improve the accuracy of stress calculations in the thread region. This approach is faster and more accurate than the previous Bolt Model 1 technique, resulting in a reduced computational cost.
What is the best approach to modelling bolts?
There is no one definitive answer to this question as the best approach may vary depending on the specific bolt geometry and simulation requirements. However, some key factors to consider when modelling bolts include: how accurately you need to simulate the bolt behaviour; how detailed your contact and analysis settings need to be; and which drafting and graphics tools are available to you. Below we provide eight methods for modelling bolts in ANSYS 15.0. Each method has its own advantages and disadvantages, so it is important to selecting the right approach for the specific scenario being modeled. Method 1: FBD Meshing One of the most popular approaches for modelling bolts is using FDD meshing. This technique can achieve high levels of accuracy by taking into account all of the internal details of a bolt, such as its roundness and dimensions. Additionally, FDD meshing can be easily configured to generate accurate contact and Analysis results. However, FDD meshing does have some limitations
What's new in ANSYS mechanical?
1) Unlimited modeling possibilities with journaling and scripting in the Mechanical interface 2) Increased meshing efficiency and quality for shell meshing 3) New CAD options for: gantry reach, machine length, rotational positioning accuracy and shear force 4) Support for User Defined Materials (UDM)
What's new in ANSYS Maxwell?
ANSYS Maxwell is a new reduced order model on poly-phase electrical machine design integrated into larger electric drive systems. ANSYS Simplorer/Ansys TwinBuilder push-back excitation capability enables open-loop simulation in Maxwell transient design for busbar applications.
What's new in ANSYS 2021 R2?
With ANSYS 2021 R2, we continue to expand simulation capabilities and ease of use for every engineer to unlock innovation and increase productivity throughout the product development process. In addition, every analyst can now benefit from Ansys Discovery’s geometry modeling workflows, groundbreaking Discovery Live physics and innovative user interface. Highlights include: Geometry Modeling Workflows: Our geometry modeling workflows provide a more efficient way for engineers to design and analyze geometric shapes. These workflows include our newly introduced Sketchup-integrated Design Studio and our intuitive Edge model editor. Our new GPUs are specifically designed for robust geometric modeling performance, letting users speed up their workflow by extracting features faster and reducing the need for manual cleanup. Discovery Live Physics: With our new Discovery Live physics engine, analysts can see how physical objects interact with each other in real time, eliminating the need for tedious postprocessing. This allows them to quickly identify problems early in the design process, saving time and money
Sources
- https://www.reddit.com/r/findanyhow/comments/wzsetr/how_to_simulate_bolt_thread_ansys_orientation/
- https://www.youtube.com/watch
- https://www.youtube.com/watch
- https://www.eng-tips.com/viewthread.cfm
- https://www.finiteelementanalysis.com.au/featured/an-overview-of-methods-for-modelling-bolts-in-ansys/
- https://www.youtube.com/watch
- https://interconex.edu.vn/us/21-how-to-simulate-bolt-thread-ansys-orientation-hienthithang-hienthinam/
- https://forum.ansys.com/forums/topic/bolt-thread-geometry-correction/
- https://courses.ansys.com/index.php/courses/modeling-the-bolt-and-preload/lessons/bolt-pretension-object-lesson-3/
- https://simutechgroup.com/modeling-bolt-threads-using-contacts-instead-of-thread-geometry/
- https://justreviewit.com/how-to/how-to-simulate-bolt-thread-ansys/
- https://qaasimeleanora.blogspot.com/2022/11/how-to-simulate-bolt-thread-ansys.html
- https://forum.ansys.com/forums/topic/analyzing-the-tightening-of-a-bolt/
- https://www.eng-tips.com/viewthread.cfm
Featured Images: pexels.com