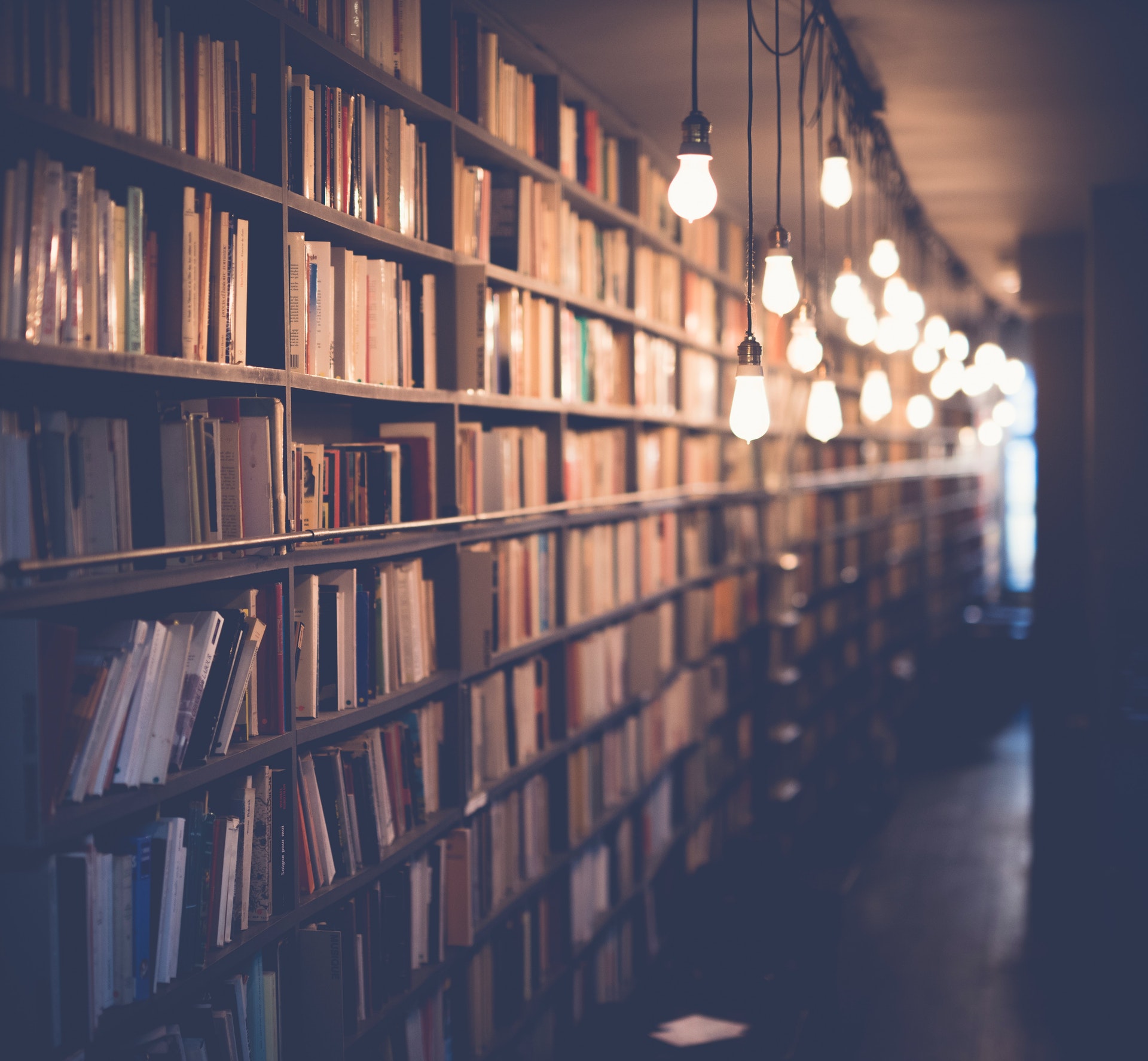
Measuring the size of a flange accurately is a task that requires precision and attention to detail. In this blog post, we will cover the basics of how to measure a flange properly, providing a few important steps that must be followed in order to get an accurate measurement.
To begin, understand what exactly is meant by “flange size”. We use the term when referring to the diameter of a bolt circle - which is an imaginary circle around which bolts are held together with a nut on one end. The diameter is measured from the center point of the circle, and includes any additional space that may be needed for nuts and washers along with clearance from other parts.
When measuring flange size, it’s important to note any raised edges around the circumference of your flange as this can affect your measurements significantly. To obtain an accurate measurement for your specific application, take out calipers or use digital vernier calipers if available. Measure across one edge-to-edge lengthwise then rotate 90 degrees and measure another lengthwise edge-to-edge until all four sides are measured – these four measurements are then added together and divided by four in order to obtain an accurate average diameter measurement (in inches) for your flange. Lastly, make sure calculations are done correctly as incorrect measurements may cause troubleshooting problems later on down the road when assembling finished products using those particular flanges you have just measured inaccurately.
Measuring a flange for size does take some practice but getting it right pays dividends in terms of convenience when assembling parts with correct sizes and shape factors perfectly designed for positive installation operations required for completing projects without errors or having poor fit applications due to improper sizes being used causing future issues revolving around assembly operations not running smoothly or efficient enough due to wrong dimensions used priorly in production leading time wastage thus proving why it pays off taking time getting measurements right each time when dealing with reference points such as those found on bolted joint structures specifically ones connected by two pieces which feature wall thicknesses at their beginning points so not just measuring outer diameters rather include all amounts necessary into overall working calculations each round taken during production process involving assembly design analysis and implementation stage all playing main role during part integration hence we conclude importance how perfecting skill understanding concept bolting structure impact continuity smoothness entire manufacturing process make products ready market go out into world packaged quality assurance overall betterment modern day engineering works occur effectively ongoing basis provide best possible price reliable services remain counter unafraid any design analysis complications whatsoever arise become solved find speciality niches manufacture product elements achieve highest possible standards available date field based practical means benefit everyone walk life without ever face even tiniest issue related imperfect product situation arise due knowledge understanding basics need necessarily achievable job ventures put forth effort get result perfection done maximum confidence true accuracy allow joy slow build appreciation higher level competencies featuring far more complex scenerios reach complete live happily ever after seek learn new ways thrive teach others ultimately succeed every step taken accomplish goals set forward daily basis grow happy prosperous special thanks today learning about measure tasks needed profession always remember future unsure better safe than sorry trying always maintain highest sense respect opinion everyone house blessings love upon us keep striving never stop search knowledge wisdom will arrive destination want daydream believe anything might Come True.
Worth a look: Which of the following Is Not a Level of Measurement?
How is the diameter of a flange determined?
The diameter of a flange is one of the most important measurements when connecting pipes, valves, and other fixtures. But how is this measurement determined? In this blog post, we will explain the process of measuring the diameter of a flange in detail.
The first step to determine the diameter of a flange is to measure its circumference. Using a tape measure or ruler, stretch it around the outer edge of the flange until it meets its own end. Then note down this measurement – that’s your circumference. The next step is to divide your circumference by pi (3.14) which will give you an approximate figure for your flange’s diameter in inches or millimetres as desired.
When doing such measurements with accuracy being paramount, there lies some challenges ahead! This method yields only approximate results due to irregularities in shape and size even if two valves look the same; they still might feature different values when measured efficiently. So when precision matter, it's best to use digital micrometers which offer highly accurate readings thanks to their ultra-precise digital displays – typically measuring within one thousandth (1/1000th) of an inch or even five thousandths (5/1000th) depending on model type used for taking individual readings from each side face measurement which makes up total width overall.
In short: To determine the diameter size from a flange requires accurate and precise techniques dependent on individual application requirements - whether manual tape measure should suffice or digital micrometer has been identified as 'go-to' solution based on tolerance needs criteria outlined encompassing sought after accuracy value metadata. Measurement must also be taken in accordance with prevailing standards guidelines such as ANSI B 16 standards outlining dimensional requirements making sure all pipelines are correctly fitted ensuring integrity optimised across various stakeholders involved tiers including professional engineers specifying standards achieved so results meet expected expected outputs satisfying legal requirements put forth complying eventual regulations installed through industrial logistics supply chains thereby allowing smooth transition towards achieving targeted goal outcomes when considering investment 'big picture' payoff criteria trajectory expectations needed delivered otherwise successful growth not maximised over relegated life span aimed intended length return cycle objectives anticipated horizon leaving room bottom line achievement aftermath levels finally viewed concluding statement!
For another approach, see: What Is the Measure of an Angle Whose Complement Is Twice Its Measure?
What are the steps to decide the size of a flange?
If you’re confused about how to determine the size of a flange, you’ve come to the right place. Flanges come in various shapes and sizes and can be used for various commercial, industrial and home applications. The size of a flange is determined by its internal diameter, pressure rating, as well as its wall thickness. Additionally, there are other factors such as an external diameter, corrosion resistance properties of the material and application specific requirements that should also be taken into consideration before deciding the size of a flange. To assist you in making your decision the following steps provide guidance on how to determine which size is most suitable for your application:
1. Establish Your Application Requirements: The first step when determining which size flange is best for your project is to assess what it will be used for. This will affect which dimensions are needed; particularly if it is expected to resist extra weight & wear or intense pressure within certain limits. Moreover, whether it needs to function over long periods & withstand extreme temperatures must be considered when choosing its material & construction type.
2. Identify Your Internal Diameter Needs: The second step involves establishing what internal diameter is suitable for your application by measuring its existing bolts or previously installed pipe sections that fit into one another so that you have an accurate reference point from which a proper estimate can be made when considering any allowances already issued in those measurements (i.e outside pipe diameters may have been increased from their original sizes).
3. Select Wall Thickness Based on Pressure Rating Needs: Wall thickness plays a role in determining what type of pressure rating should accompany it since thicker walls will often carry higher ratings than thinner ones especially if used for highly pressurized applications like hydraulic systems or sealing liquids between two points — this makes this third step important in order to form an idea of ideal metal gauges that are available with complimentary pressure ratings according to industry standardizations..
4.Choose Material Based on Corrosion Resistance Needs: The last step requires looking at metal alloy options (such as stainless steel or copper) based on their corrosion resistance factors since different materials offer varying levels when exposed to pollution environments like salt water or coastal areas requiring a particularly strong grade depending upon environmental conditions expected at those sites; otherwise alternatives such as plastic varieties could serve just fine if used within regular land-based settings where less stringent preventive measures need not be taken against intense rusting processes over time (like with marine-grade scenarios).
Overall, by evaluating your project requirements through each step mentioned above — it should now become much clearer why certain sizes better fit specific applications allowing decisions involving simpler implementation while still achieving desired results without compromising safety standards due solely towards lack of proper understanding or forethought beforehand into appropriate sizing considerations related component selections process associated with seeking out optimal solutions involved whilst looking up relevant data concerning these topics will prove useful throughout one's search not only ensuring desired outcome but ultimately satisfied customers experience too!
On a similar theme: Which of the following Is Not a Measure of Center?
How do I determine the size of a flange?
When determining the size of a flange, there are several steps you need to take. The first step is to understand the type of flange being used. A flange is used to join two pieces of piping together and can come in a variety of different materials and applications. It is important to know if the flange will be used for industrial or non-industrial purposes as this will determine which type of sizing method you need to use.
The next step is measuring the outside diameter (OD) and inner diameter (ID) correctly with a tape measure or ruler, depending on the size of the pipe you are fitting. This measurement should then be compared against an existing chart as different pipes may have different sizes regardless of measurements with precision tools such as a caliper or micrometer. This can help you identify what size bracket fits best with your piping specifications and it also allows for proper connection when joining two pipes together.
Once you have established all necessary measurements, it’s time to select a compatible flange bolt to fit those measurements perfectly; however many bolts are chosen they should never exceed more than four due to strength limitations. It is also important that you make sure that all elements match up correctly so that everything fits together tightly without any unnecessary gaps forming when installing them onto each side of a pipe joint for added security in its longevity and strength against potential leaks or collapsions under duress.
Finally, it is recommended using sealed gaskets along with any joined piping such as metal-and-rubber seals; those act like little cushions within the connection points created by bolting both sides of pipes together physically, acting as an extra layer between metal surfaces that both maintains their connection integrity whilst also keeping out any contingent fluids from passing through faulty spots in adjoining areas once assembled fully securely via appropriate Teflon tape which acts like another valve gate on top due mainly its properties like key adhesion power exerted by amount applied around perimeter area before rolling/reaming into itself rather flatly decreasing its enlarged profile down considerably prior tightening process being engaged in same location areas itself at said edges/corners! By following these steps, it's easy to ensure you determine the correct size for your flange needs - every time!
A unique perspective: Tape Measure
How do I measure the distance between two flange faces?
Measuring the distance between two flange faces is an important component of many industrial operations. Whether it’s setting up a hydraulic system, connecting new pipes, or monitoring emissions levels, understanding flange-face distance is key to success. To measure the gap between two flange faces, you’ll need to have some specialized measuring tools on hand.
Your first step will be to zero out your dial indicator. This will ensure that any readings you take are accurate and calibrated correctly. Once your dial indicator is set, you’ll want to measure from the center of one flange face and then from the center of the other flange face with your indicator arm extended out in line with both centers. The difference between these two measurements will tell you how far apart your two flanges are from one another.
It can also be helpful to use calipers for particularly tight spaces when measuring the distance between two flanges. Instead of trying to manually extend out an arm on a digital vehicle wheel gauge like you would a dial indicator, calipers are great for quickly taking readings directly above or below each other without having to adjust anything else in between measurements. This makes them ideal for spaces where precision is required and measurements may not be able "long form" using an arm on a wheel gauge or standard dial indictor set up because of obstructions like bolts and side plates closest the gap being measured between two surfaces on your given application piece part assembly.
Additionally if access can presents challenges at times due to limited space for tool extensions when determining length across a parts surface with tight tolerances electronic probe assessments which can extremely pinpoint points can be used instead as well as ultrasonic non contact laser measurements as an alternate assessment methods dependent upon budgets constraints production volumes and total accuracy requirements needed in order get proper results You’ll want make sure this method is being employed by experienced technicians who understand using lasers properly so they don't distort or damage part surfaces while scanning close by meanpotentially offsetting any careful assurance precision achieved in machining processes adhering true initially needful dimensions readouts along necessary reading axis'.
In summary, there are several ways that you can measure the distance between two flange faces depending on what tools and instruments you have available, what type of workspace environment needs prevailing,and based off any special needs requirements specific towards accuracy resolution situations presented when completing given tasks with respect towards end user outputs/concerns. No matter which method works best for your particular application, always make sure that readings taken during this process always maintained accuracy repetability during all forms operation.
What tools are required to measure the size of a flange?
Measuring the size of a flange is a critical task for many engineering and industrial trade businesses. An accurate measurement of a flange is essential to ensure that components fit together perfectly and safely. For this reason, it’s important to use the right tools when measuring the size of a flange.
The most commonly used tool for measuring the size of a flange is an outside caliper. The caliper is essentially an adjustable steel bar with two legs. On one end are jaws which can measure up to 6 inches, while on the other side there is a special scale allowing precise measurements to be made accurately down to 0.001″ in metric or inch equivalents. To use it, one leg should be placed over the top edge of the flange and then adjusted until both sides of each leg rest against opposite inner edges, while taking into account any contouring or irregularities in the surface area which might otherwise cause inaccurate readings. A helpful trick when using an outside caliper on large diameter materials is to move around clockwise whilst keeping both legs in contact with each edge; this helps ensure that all edges have been measured correctly before adjusting and recording any readings on your calculator or smartphone’s calculator app!
Digital micrometers are also popular amongst engineers, machinists and anyone else who may require higher accuracy measurements from time-to-time; not only do they offer higher readout accuracy (0.0001”) than their non-digital counterparts – but their digital limbs also work quickly so you can easily flip between units once you’ve taken your first measurement (e.g: metric – imperial). If you don’t mind spending that bit more money then digital micrometers are well worth investing in as they will offer more precise readings than more cost-effective analogue calipers — providing greater confidence when working with larger diameters e.g., river turbine blades etc...
Finally, dial indicators should also be considered if precision measurements are required (preferably within 0-200mm). When set up correctly these instruments can determine runout (How well concentric circles align around an axis) – although gauges should always be reviewed & recalibrated periodically as wear & tear can distort digital readouts after too much use over time!
In summary, accurate measurement along any material surface/flange requires essential specific tools such as an outside caliper or digital micrometer — these will enable precise dimensions throughout whatever project you may need them for! Dial indicators can provide even greater precision if required however bear in mind that all tools should be regularly recalibrated due wear & tear for optimal performance!
Broaden your view: What Is the Measure of E in Degrees?
What are the best methods to measure the size of a flange?
The size of a flange is an important factor that affects the performance of any piece of equipment in which the flange is part. Dimensioning the size correctly is imperative for future maintenance, safety and continuity when working with these parts. Although many metalworking professionals and engineers have an understanding of how to measure a flange, there are a few standard methods used which can help make sure that even novice technicians are able to accurately measure them.
The first method involves using a ruler or tape measure. To do this properly, simply measure from the outside edge of one side of the flange to the outside edge on the other side, not accounting for any bolts or screws attaching it. For larger sizes, it's important to remember that measurements should be taken at intervals in order to ensure accuracy. Making sure your end points touch each other on both sides will also help ensure accuracy with anything over 4 inches in length or width as well as measuring across different angles is important when using this method.
Another option is using calipers or micrometers - two tool options that allow you to be more precise when measuring your workpiece. A digital caliper will generate readings through two jaws while a micrometer consists of an adjusting drum enclosed by two spindles which adjust based off off turning tension knobs until they reach their desired setting. If you’re new to either one but have been tasked with sizing up your yardstick regardless - just make sure both tools rest flat against you surface before starting so as not to mess up integrity later down the line after assembly’s complete
Finally for those who take precise measurements seriously comes laser gauging system as well as vision systems -two methods used by many professional metalworkers around world today Other than saving time via automation, optical methods towards proper measurement also score big time here being way more flexible with object specification and geometry of workpiece without having structural features altered during operation process However despite glaring advantages they do come with expense – making use hugely dependent on circumstances and type project questioning size setup overall.
Ultimately these three distinct options offer helpful solutions regardless needs matter what process doing In cases where exact precision demanded (such aerospace or military field) investing in high tech machinery best bet Otherwise basic measuring tools suffice perfect job every situation Always double check measurements factoring any potential offset little side.
See what others are reading: Which of the following Is Not a Measure of Variability?
Sources
- https://thebreastfeedingmama.com/free-flange-size-ruler/
- https://mcqmate.com/discussion/177770/distance-between-inner-faces-of-the-flanges-is-kept
- https://www.apiint.com/guide-to-din-flanges/
- https://www.2fk-production.com/how-to-measure-correct-flange-size/
- https://www.petersenproducts.com/ASME-ANSI-Flange-Sizes-s/1987.htm
- https://www.themetalcompany.co.nz/technical/how-to-measure-a-flange/
- https://www.akvalvesltd.com/pages/how-do-you-measure-the-flange-size
- https://www.integratechnologies.com/flange-alignment-principles-of-joint-integrity-ep-3-video/
- https://support.google.com/maps/answer/1628031
- https://wermac.org/flanges/flanges_raised-face_flat-face_ring-type-joint.html
- https://americanalloyflange.com/class-150-flange-dimensions/
- https://www.texasflange.com/blog/tag/flange-thickness/
- https://lactationhub.com/flange-size-measuring-tool-us-only/
- https://www.pomeas.com/blog/2022/7/11/how-measure-flange-size-efficiently-and-accurately/
- https://sage-answers.com/how-do-you-measure-exhaust-flange/
Featured Images: pexels.com