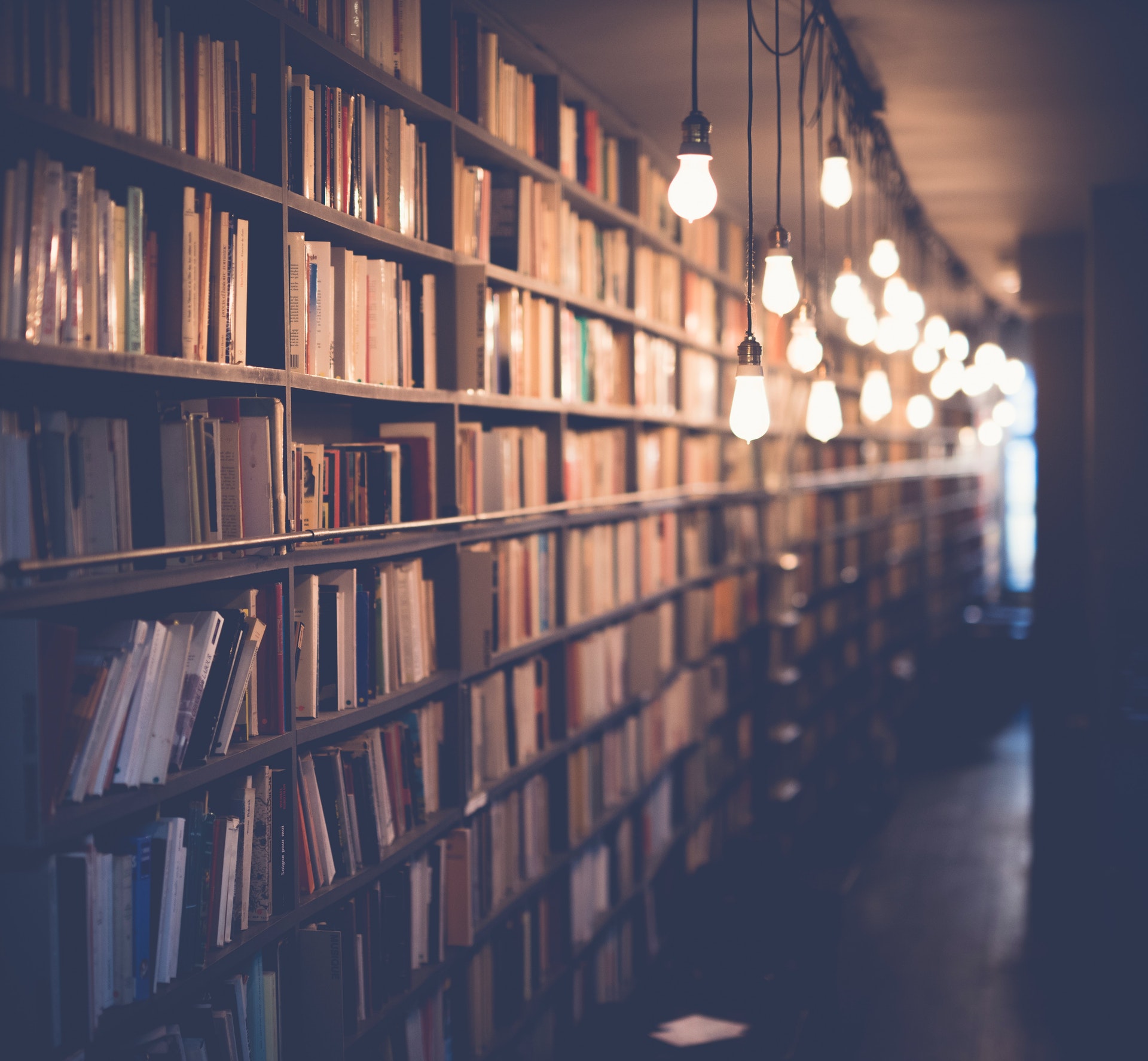
aluminum coils are used in a variety of industries for different purposes. They are used in the automotive industry, for example, in the manufacture of cars and trucks. They are also used in the construction industry, for example, in the construction of buildings. In the aerospace industry, they are used in the construction of aircraft.
Aluminum coils are made by passing aluminum ingots through a series of rollers. The rollers reduce the thickness of the ingots and shape them into coils. The coils are then passed through a series of annealing furnaces. The annealing process strengthens the coils and makes them more ductile.
After the coils have cooled, they are passed through a series of cutting machines. The cutting machines cut the coils into the desired length. The coils are then ready to be used in the various industries.
A unique perspective: Automobile Industry Considered
How are aluminum coils made?
Aluminum coils are made by passing aluminum sheet through rollers to achieve the desired thickness. The sheet is then cut to size and can be used in a variety of applications. Some common applications for aluminum coils include transportation, HVAC, and electrical equipment.
Aluminum coils are made using a “cold rolling” process, which involves passing the sheet through rollers at a temperature below its recrystallization point. This process increases the strength and hardness of the metal. The sheet is then annealed, or heat treated, to improve ductility. Finally, the sheet is cut to size and can be used in a variety of applications.
Some common applications for aluminum coils include transportation, HVAC, and electrical equipment. Transportation applications include automobiles, aircraft, and railway cars. HVAC applications include ductwork and HVAC systems. Electrical applications include electrical equipment and wiring.
Aluminum coils are a versatile material that can be used in a variety of applications. Thanks to the “cold rolling” process, they are strong and durable. They can easily be cut to size, making them a versatile option for a variety of needs.
If this caught your attention, see: What Are the Best Places to Elope in California?
What is the process of making aluminum coils?
The process of making aluminum coils is a highly efficient one that starts with the wear-resistant material being melted down and formed into large ingots. These ingots are then fed through a series of rollers that gradually thin them out until they reach the desired thickness. From there, the coils are cut to size and cooled before being ready for use.
The aluminum coils that are used in a variety of industries are a critical component in the manufacturing process. And while the process of making them may seem relatively simple, there is a great deal of precision and care that goes into every step to ensure a quality product.
The first step in the process is to melt down the aluminum. This is done in a furnace that is specifically designed for this purpose and can reach temperatures upwards of 2,000 degrees Fahrenheit. Once the aluminum is in liquid form, it is poured into large ingots that will eventually be fed through the rollers.
The ingots are then placed on a conveyor belt and fed into what is known as a breakdown mill. This mill uses a series of large rollers to slowly reduce the thickness of the ingots. As the ingots are reduced in thickness, they are transferred to a series of smaller rollers that continue the process until the desired thickness is achieved.
Once the aluminum coils have reached the desired thickness, they are cut to size and cooled. The cooling process is critical in order to prevent the aluminum from becoming too brittle. Once cooled, the coils are ready for use in a variety of applications.
The process of making aluminum coils is one that is highly efficient and results in a product that is of the highest quality. The care and precision that goes into each step of the process ensures that the end product is one that will meet the needs of the customer.
For more insights, see: What Is Friction?
What are the steps involved in making aluminum coils?
When most people think of aluminum, they think of soda cans or foil. However, aluminum is used in a variety of products and industries. One of the most common uses for aluminum is in the form of coils. Aluminum coils are thin sheets of aluminum that are rolled into a coil shape.
The first step in making aluminum coils is to create what is known as an aluminum ingot. This is done by melting aluminum in a furnace. Once the aluminum is melted, it is poured into a mold that is the shape and size of the desired coil.
Once the aluminum has cooled and solidified, it is then ready to be rolled into a coil. To do this, the aluminum ingot is placed on a large roller. The roller applies pressure to the aluminum, which cause it to flatten out into a large sheet.
This large sheet of aluminum is then passed through a series of smaller rollers. Each time the sheet passes through a pair of rollers, the rollers apply pressure and cause the sheet to become thinner. After passing through several sets of rollers, the aluminum sheet is now thin enough to be considered a coil.
The final step in the process is to cut the aluminum coil into the desired length. This is typically done with a large cutting machine. Once the coil is cut to size, it is then ready to be used in a variety of applications.
Take a look at this: Variety 2 Level 6
What are the materials used in making aluminum coils?
Aluminum coils are made from a variety of materials, including aluminum, steel, copper and brass. The most common material used in making aluminum coils is aluminum. Aluminum is a strong, lightweight and corrosion-resistant metal that is easy to work with. It is also an excellent conductor of electricity and heat. Steel is another common material used in making aluminum coils. Steel is strong and durable, but it is also heavier than aluminum. Copper and brass are also sometimes used in making aluminum coils.
Check this out: Brass Knuckles Illegal
What is the machinery used in making aluminum coils?
There are a few different machines that are used in the manufacturing process of aluminum coils. The first machine is called an aluminum melting furnace. This furnace is used to melt the aluminum so that it can be formed into coils. The aluminum is melted at a high temperature, usually around 2000 degrees Fahrenheit. Once the aluminum is melted, it is poured into a mold. The mold is a long, thin cylinder. The aluminum is then cooled and formed into a coil.
The next machine that is used is called a cold rolling mill. This machine is used to flatten and smooth the aluminum coil. The coil is passed through the mill several times. The rollers in the mill get smaller each time the coil is passed through. This process makes the aluminum thinner and smoother.
The last machine that is used is called an annealing furnace. This furnace is used to relieve stress in the aluminum. The aluminum is heated to a high temperature and then cooled slowly. This process makes the aluminum stronger and more flexible.
Aluminum coils are used in a variety of industries. They are used in the automotive industry for making car parts. They are also used in the construction industry for making gutters and downspouts.
Check this out: Water Cooled Ice Machine Work
How is the aluminum coil made?
The aluminum coil is made by taking a large round disk of aluminum and running it through a series of rollers. The rollers flatten the disk out into a large sheet. The sheet is then fed through a series of progressively smaller rollers. This reduces the thickness of the sheet until it is the desired thickness for the aluminum coil. The sheet is then cut to size and the edges are trimmed. The aluminum coil is then ready to be used.
Related reading: Coil Pack
What is the process of making an aluminum coil?
The aluminum coil is made up of a series of aluminum plates that are stacked on top of each other. The plates are then welded together at the seams. The welding process is done by an automated machine that uses a high-powered laser to weld the seam. Once the seam is welded, the aluminum coil is then cooled and trimmed to size.
For your interest: Dirty Condenser Coil
What are the steps involved in making an aluminum coil?
Aluminum coils are used in a variety of industries, from automotive manufacturing to the construction of electrical transformers. The process of making an aluminum coil begins with the aluminum ingot, which is first melted and then cast into a long, cylindrical shape. Once the aluminum ingot has cooled and solidified, it is fed into a rolling mill, where it is slowly flattened into a large sheet.
After the aluminum sheet has been rolled to the desired thickness, it is then passed through a set of rollers that gives it a uniform shape. Next, the aluminum sheet is fed into a machine that cuts it into strips of the desired width. These strips are then wound into coils and passed through a series of heaters that raise the temperature of the aluminum to the point where it can be easily formed into the final shape.
Once the aluminum coil has been formed, it is then passed through a series of cooling chambers that help it to retain its shape. Finally, the aluminum coil is cut to the desired length and then packaged for shipment.
A different take: Find Tungsten Ingot
What are the materials used in making an aluminum coil?
An aluminum coil is a metal product that is made by passing an aluminum ingot through a rolling mill to produce a long, coiled strip of metal. The ingot is first heated to a temperature that is above its recrystallization temperature, which is the temperature at which the metal’s grains begin to grow. The metal is then passed through the rolling mill, which reduces the thickness of the metal and causes the metal’s grains to become elongated. The process is then repeated until the desired thickness is achieved.
Aluminum coils can be used in a variety of applications, including automotive, construction, and consumer products. Automotive applications for aluminum coils include body panels, engine components, and transmissions. Construction applications for aluminum coils include roofing, siding, and gutters. Consumer applications for aluminum coils include appliances, utensils, and packaging.
Aluminum coils are made from an aluminum alloy that contains at least 92.5% aluminum. The other elements in the alloy can include copper, manganese, silicon, magnesium, or zinc. The aluminum alloy is heated to a temperature that is above its recrystallization temperature, which is the temperature at which the metal’s grains begin to grow. The metal is then passed through the rolling mill, which reduces the thickness of the metal and causes the metal’s grains to become elongated. The process is then repeated until the desired thickness is achieved.
Aluminum coils can be used in a variety of applications, including automotive, construction, and consumer products. Automotive applications for aluminum coils include body panels, engine components, and transmissions. Construction applications for aluminum coils include roofing, siding, and gutters. Consumer applications for aluminum coils include appliances, utensils, and packaging.
Here's an interesting read: Rebuilds Manual Transmissions
Frequently Asked Questions
How is aluminium made from cryolite?
Electrolytic reduction is a process where an electric current is used to cause metal atoms to lose electrons, and eventually form a new metal. In the cryolite-bauxite-alumina production process, an electric current is passed through the mixture of cryolite and bauxite in order to strip away the aluminium atoms.
How is alumina made?
Alumina is made from the mineral alumina. This mineral is usually found in the form of small, black, pieces. After being mined, the mineral is crushed into very small pieces and mixed with a set of other chemicals. The mixture is then heated until it turns into a hot liquid. The liquid alumina is poured into molds while it's still hot. The molds are cylindrical and have many sharp edges. The molten alumina quickly cools down and forms these sharply angled walls around the mold.
How is aluminium made from bauxite?
Aluminium can be made from bauxite by three primary stages: alumina production, aluminium oxide production, and pure aluminium production. In the alumina production stage, bauxite is processed into alumina. In the aluminium oxide production stage, alumina is processed into aluminum oxide. Finally, in the pure aluminium production stage, aluminum oxide is broken down into its components using electric current.
What is an aluminum alloy?
An aluminum alloy is a composition consisting mainly of aluminum to which other elements have been added. The alloy is made by mixing together the elements when aluminum is molten (liquid), which cools to form a homogeneous solid solution. Aluminium alloys are typically composed of about 12% magnesium and 8% silicon. What are the different types of aluminum alloys? Aluminum alloys can be classified according to their chemical compositions and physical properties. Among the most common types of aluminum alloys are: aluminums, bronzes, alloys with titanium, manganese, and molybdenum, and brass.
How is aluminium made?
Aluminium is made from bauxites, a mineral which is rich in aluminium. First, the bauxite ore is mined, and then it is converted into aluminium oxide using oxygen gas. Aluminium oxide is then reduced using electricity to produce aluminium.
Sources
- https://www.alumhm.com/a/the-manufacturing-process-of-mill-finish-aluminum-coil.html
- https://www.youtube.com/watch
- https://www.aluminum-alloy.com/aluminum-coil-manufacturing-process.html
- https://www.hm-alu.com/a/what-is-manufacturing-process-of-prefinished-aluminum-coils.html
- https://www.quora.com/How-do-I-produce-an-aluminium-coil-strip
- https://quizlet.com/300343610/thermal-energy-lesson-3-conduction-flash-cards/
- https://brainly.com/question/21335685
- https://www.wanstaraluminumgroup.com/news/what-are-the-processing-processes-of-the-surfa-62802159.html
- https://www.youtube.com/watch
- https://www.iqsdirectory.com/articles/aluminum-metal/aluminum-coil.html
- https://en.asriportal.com/10637/how-do-the-metal-aluminum-coils/
- https://www.youtube.com/watch
- https://www.aluminum-coil.net/aluminium-coil-weight-and-thickness.html
- https://www.vespolari-steel.com/news/The_production_process_of_aluminum_coil.html
Featured Images: pexels.com