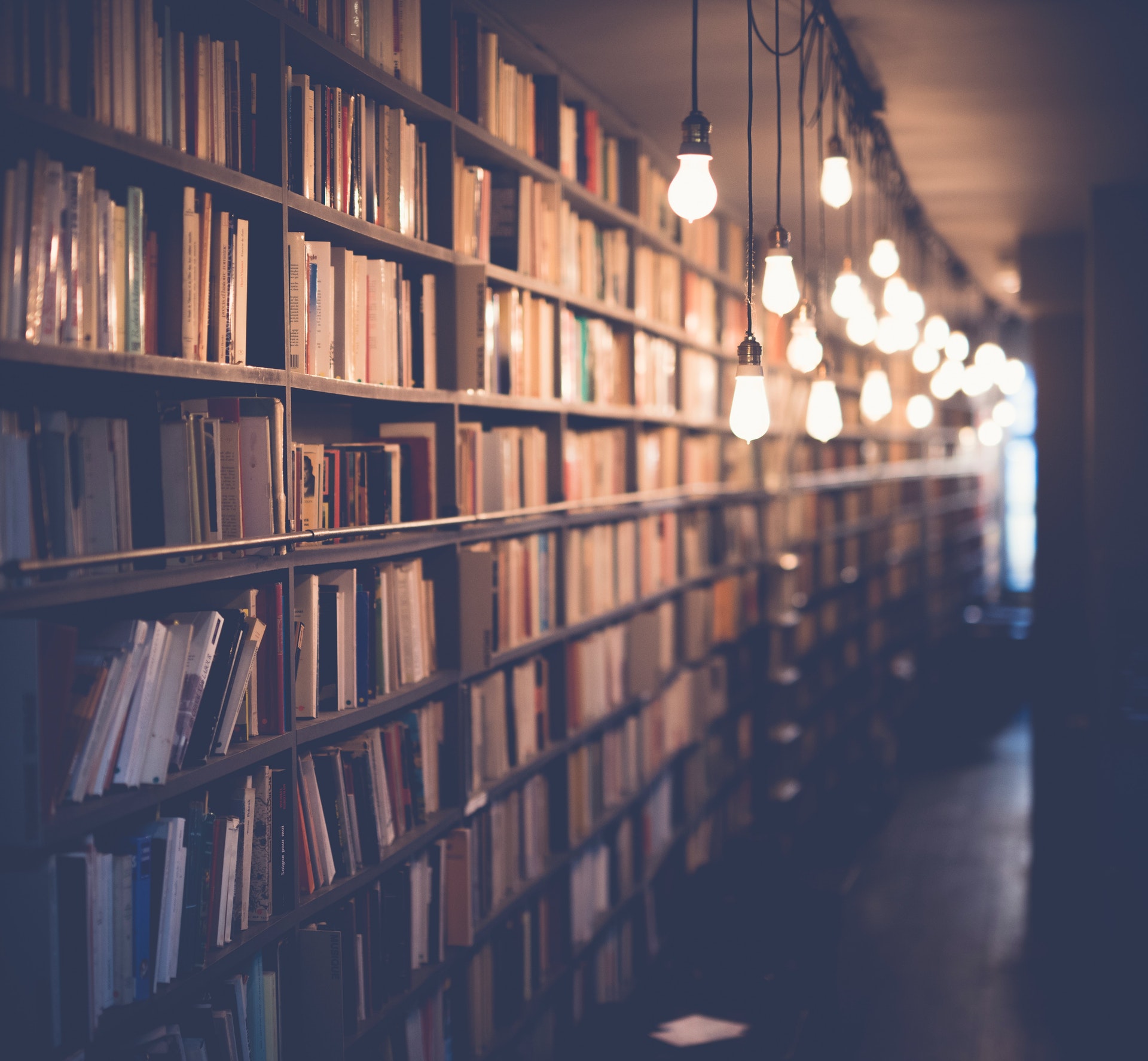
Converting equipment is the machinery involved in converting a particular material from one form to another. This process can involve anything from turning paper into cardboard boxes or packaging, to blending ingredients, to cutting fabrics. It’s a wide step of machines and processes that take raw materials from their original state and transform them into something new and different.
The key to successful converting depends largely on the type of material being processed and the equipment used throughout the process. This could include cutting machines, printing presses, labeling machinery and heat treatment units which are all used depending on what needs to be transformed. While some kinds of conversions require manual labor, automated machines allow for large scale industrial production resulting in greater accuracy and better yields with less downtime due to errors during conversion steps.
Once a desired product is produced, it is necessary for operators to visually check all parts before packing them away so that customers can be sure they’re receiving exactly what they ordered without any defects or inaccurate measurements. Additionally, since food sectors must fit tight Health & Safety regulations it’s necessary for all pieces of equipment used during conversion stages meet industry standards too.
From pharmacy products through simple paper goods up to vast industrial scales – effective operating converting equipment ensures these unique producible requirements are met every time!
What is a converting machine?
A converting machine is a piece of equipment that can be used to change one type or form of energy into another. For example, a generator converts mechanical energy into electrical energy, while an electric motor turns electricity into kinetic energy. Likewise, fuel cells convert chemical energy from hydrogen and oxygen into electrical power. Converting machines are essential components in many industries such as automotive, aerospace engineering, industrial manufacturing and more.
Converting machines come in many forms both mechanical and electronic each designed to carry out a specific task or process and the requirements for each vary greatly depending on the particular application they are intended for. Generally speaking however all converter machines will have certain basic elements in common including an input channel through which the desired form of power is introduced to the device as well as output channels from which various products of conversion are emitted after being subjected to various kinds of processing techniques and transformations within its interior components or systems.
The most commonly used converting machines include transducers that transform physical quantities such as force, pressure or displacement into electrical signals; Inverters that can handle AC currents; frequency converters; converters for pulse width modulation ; signal conditioners like amplifiers, filters etc ; AC/DC voltage converters & regulators ; DC current regulator & stabilizers along with tactical robotic arms. These sophisticated tools cater to a broad range of needs across different sectors but might also contain universal elements found in every unit depending upon its purpose - some examples include rectifier diodes, inductors, transformers & switches. In conclusion it is safe to say that regardless of industry, there exists some kind of base level converter machine so versatile it can meet any need regardless challenging task presented by today’s applications.
Related reading: Sell Catalytic Converters
What is a converting system?
A converting system is a tool that enables businesses to convert visitors to customers. This can be done through various marketing tactics, such as segmentation, analytics, dynamic display ads, personalization, and optimization. By addressing user needs and providing customization options for the user experience, these conversion systems help boost business performance by bridging the gap between interested consumers and actionable buyers.
In simple terms, a converting system refers to any process or strategy used by marketers to turn visitors into customers by molding their experience with a product or service and providing them with personalized content that are tailored towards their needs. Essentially, this technology helps businesses increase online conversions and sales while still delivering engaging customer experiences at scale.
Overall, implementing an effective conversion system is key for increasing website visits over time. As such techniques continue to evolve in today's digital landscape - where making data-driven decisions based on user preferences has become the norm - savvy businesses should consider utilizing converting systems that enhance the customer journey so they don’t get left behind!
You might enjoy: Conversion Ratio for Convertible Bonds
What are the components of a converting system?
It’s important to understand the components of a converting system if you want your business to succeed. The components of such a system include sales funnels, lead magnets, lead nurturing emails, and split testing.
Sales Funnels: This core component creates an automated process that encourages prospects to purchase your offers. A sales funnel is typically divided into different stages; these stages generally start with generating leads, then move onto building relationships and engaging those leads in meaningful conversations, and ultimately converting those leads into customers. With effective sales funnels in place, creating profitable outcomes can become more predictable and easier to manage.
Lead Magnets: To ensure that people give you their contact information you must offer them something valuable up front. Lead magnets might be anything from a downloadable guide or pdf to an exclusive video series or discounted trial offer; whatever it is should provide something valuable for them in return for their contact information. You’ll want to create enticing lead magnets that will motivate people enough so they give away their contact information willingly right after viewing it.
Lead Nurturing Emails: Once you have the contact details of prospective customers they must be nurtured over time with helpful emails until they are ready to buy from you – this is what is known as email marketing or email automation software like ConvertKit or Infusionsoft. Automation software allows marketers can segment audiences based on the actions taken (or not taken), host events for future buyers and increase customer interaction – without having to do all the work themselves! In this way automation helps build relationships with potential customers which are critical for conversions over time!
Split Testing: As marketers set up optimization campaigns it may become necessary at times during various growth stages/scenarios that demand additional experimentation as certain elements regularly need re-evaluation - this practice of trialling different versions of an online landing page through “split tests” often provides statistically safe results so choices can be made accordingly while considering cost effectiveness too – services like Visual Website Optimizer help marketers compare variations side by side often bringing new insights on how best improve conversion rates where clearly objective measures are needed instead subjective opinions determining strategy implementations especially when unsure what else could result in better performances given limited budgets plus creative/time resources available... Trial & error ultimately rules supreme here guiding us towards optimal solution(s)!
All in all, understanding the components involved in a successful converting system will help create lasting success for any business looking maximize profits while satisfying its customer base at same time!
You might like: Equipment Rental Business Insurance
What are the purposes of converting equipment?
Converting equipment helps to make production processes more efficient and cost-effective, contributing to the profitability of a business. The purposes of converting equipment vary depending on the type and setting of adoption but may include tasks such as combining multiple functions into one, streamlining operations and increasing productivity or output.
One way converting equipment can improve operations is by combining multiple procedures into one process. Manufacturers, for instance, often require separate machines for cutting, processing and sealing plastic film packaging but can use a converting machine capable of performing all three tasks in one system instead. This reduces setup times and upstream costs associated with larger equipment sets which makes the overall production process faster.
Converting machines may also allow organizations to rapidly expand their products or services within an industry with minimal added costs as compared to purchasing entirely new machinery each time a manufacturing element needs changing or updating. Converting machines are able to adapt quickly by being equipped with flexible parts that allows them to be removed and adjusted according interchangeable tools required for specific job elements without needing an entire machine reset until major adjustments are needed again at some point down the line. Such like versatility leads reduced downtime when changes need implementing - leading faster turnarounds intervals in terms of output delivery.
Finally, because many types of converting machinery are built out of modular designs that come in custom sizes based on anticipated needs – businesses do not have pay for oversized models upfront when getting started – reducing both initial investment costs along with subsequent servicing fees overtime as individual parts can be replaced at relatively low prices if wear issues occur over a lengthy period usage. With this flexibility giving companies much needed pricing relief from further investments down road - ultimately offering long timeframe cost benefits too.
On a similar theme: Caterpillar Equipment Cost
How does converting equipment work?
When it comes to converting equipment, the process can be a bit complicated. But, understanding how this type of technology works is essential for anyone who needs to convert materials from one form to another in an industrial setting.
Basically, converting equipment uses force in order to transfer the material from its original form into a new shape and structure. This process is most often used with paper and plastic since these types of materials are malleable enough to conform into different shapes through pressure or heat. To begin, the material is fed onto a conveyor belt where it will then go through a series of rollers with specific dimensions that will shape and flatten the material out before it goes further along its path.
Once it reaches the conversion stage, special machines will apply pressure as well as heat in order to stretch and mold the material into whatever shape it is intended for; such as bags for packaging or boxes for shipping. It’s worth noting that depending on how complex or unique a conversion you require, additional machines may be needed in order to achieve your desired result: some machines are used exclusively for folding while others are able seal according strict specifications you give them.
Ultimately, this entire process depends on having detailed instructions regarding what type of product should be produced so that all machine parameters remain consistent throughout production ensuring quality control over every step which ultimately ends with an end product that meets all requirements set out before hand – whether its strength requirements or certain aesthetic criteria -while also conserving both time and resources during production too!
What are the different types of converting equipment?
When it comes to converting equipment, there are many different types available on the market today. Depending on the needs and requirements of your facility, it is important to understand the differences between each type in order to determine which one best suits your needs.
Converting machines can be split into two main categories: Rotary and Flatbed Machines. Rotary machines are used for a variety of applications across multiple industries and involve a continuous cutting process that uses rotating contours that follow pre-programmed patterns. Rotary machines come in three different types; die cutting, laminating and matrix removal machines. Die cutters use sharp steel dies with raised surfaces or designs to cut through materials with varying levels of pressure depending on the material’s thickness; laminators use adhesive technologies to laminate materials such as fabrics and paper before creating prints or labels; matrix removal machines can be used for removing cardboard liner from stickers prior to printing or finishing operations.
Flat bed Machines typically provide faster outputs than rotary conversion machinery due its large flat bed surface area that allows large runs of material as well as a continuous flow production process allowing more pieces per hour can be created compared to rotary machinery. Some flatbed converting machinery includes laser cutting systems which make precise cuts by directing highly focused beams at specific points on the material being processed along with routing systems which use high speeds routers operating in two heating beds providing both CNC trimming and patterned routing functions often at speeds up to 500 m/minute! Close tolerance requirements are also achievable using flat bed systems due their intricate cutting quality options including drilling five times faster than conventional electric drills, semi-automated folding stations for flexible substrates as well as multiple roll feeders for laser cutting or engraving purposes without manual intervention meaning high precise output with repeatability is possible every time!
Finally specialty finishing processes include engraving using multi-axis lasers selectively removing layers from certain areas while leaving other areas untouched while embossing techniques create decorative relief images via stamping technologies similar techniques commonly used create trade marks onto leather surfaces etc whilst stamping technologies work by pushing objects forcibly against each other under mechanical pressure so that markings appear on both surfaces ensuring intricate & precise patterns are achievable every time within smaller tolerances giving professionals an end product they know they can rely upon!
In conclusion there is no doubt that all these varying kinds of converting equipment have markedly transformed whole industries ushering new levels of efficiency, accuracy & cost effectiveness & providing customers everywhere something unique compared what was once achievable streaming costs downwards allowing people access unique services rarely thought possible prior this revolutionary event!
Intriguing read: Used Equipment Financing
Frequently Asked Questions
What is a conversion?
Simply put, a conversion is an action taken by a website visitor that is considered profitable for the website’s owner - and which is encouraged through CTA messages.
What is an example of a converter?
A converter’s equipment might take a web of plastic film, cut it into lengths, and fuse their edges, thus converting it into plastic bags.
What is the converting process in packaging?
The converting process in packaging typically involves more than one process or step that may include film formation, orientation, metallization, lamination, coating, printing, winding, and slitting.
What are the different types of converting processes?
There are five main converting processes: hot melt coating, gravure coating, curtain coating, slot-die coating and rotogravure (gravure) printing.
What does it mean to “convert” material?
When material is converted, it undergoes a physical, chemical or biological change which alters its characteristics.
Sources
- https://sage-answer.com/what-is-a-system-conversion/
- https://clouglobal.com/what-is-a-power-conversion-system-pcs/
- https://www.lawinsider.com/dictionary/conversion-equipment
- https://alemo.eu/converting-machinery/
- https://www.answers.com/engineering/What_is_a_converting_machine
- https://www.youtube.com/watch
- https://pace-equipment.com/converting-machines/
- https://davis-standard.com/converting-systems/
- https://www.convertingsystems.com/
- https://knowledgeburrow.com/what-is-system-conversion-and-its-types/
- https://www.tecnocut.com/en/converting-equipment/
- http://blog.focuslabel.com/a-brief-guide-to-label-converting-machinery
- https://southshorecontrols.com/what-is-web-converting-understanding-web-converting-equipment/
- http://www.rolltorollprocessingmachines.com/converting.php
- https://info-web-portal.com/qa/what-is-a-system-conversion.html
Featured Images: pexels.com