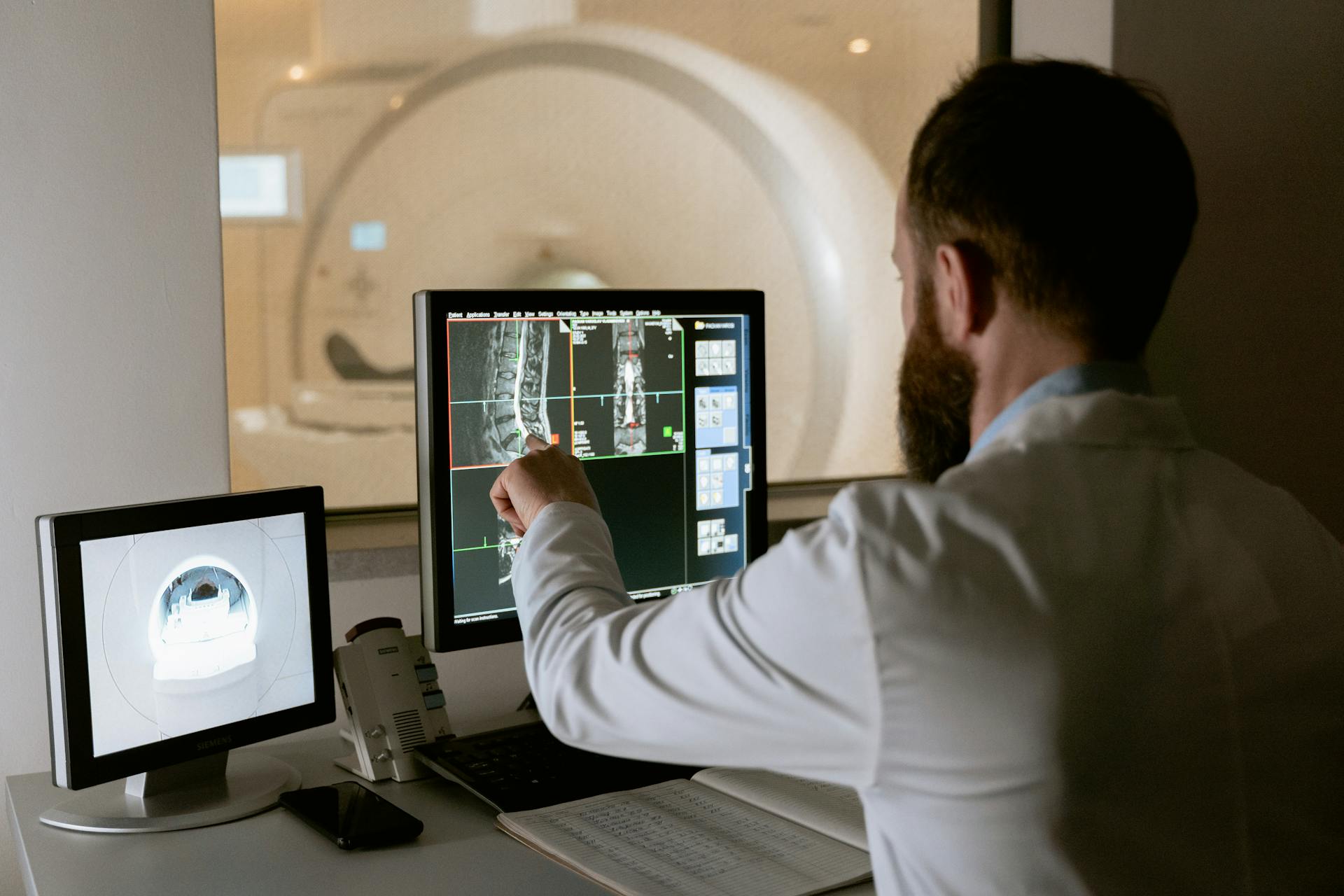
Hazard identification is a proactive approach to identifying potential hazards before they cause harm.
The process involves looking for potential sources of harm, such as chemical substances, physical objects, or environmental factors.
A hazard can be any situation or thing that has the potential to cause harm, injury, or damage.
In a workplace setting, hazards can include equipment malfunctions, slips, trips, and falls.
Risk assessment is a critical step in identifying potential risks associated with identified hazards.
For example, a chemical substance can be a hazard, but the risk of injury from it depends on how it's handled and the precautions taken.
A risk can be a combination of the likelihood of a hazard occurring and the potential impact on people or the environment.
What Is HIRA?
HIRA is a systematic approach to identifying potential hazards and assessing the risks associated with them. It's a two-step process that starts with identifying potential hazards within a process.
Explore further: Risk Assessment Process Steps
The initial focus of HIRA is to identify potential hazards, which is the first step in the process. Regular inspections are necessary to identify these hazards.
A comprehensive guide to HIRA is essential for building a foundation for future policies. This guide should clearly state what the organization should conduct for an adequate and successful HIRA.
The guide should include a checklist of steps such as regular inspections, hazard analysis, and incident investigations to identify hazards. Documentation of possible changes in design, operations, etc. is crucial for future transparency.
A step-by-step guide to HIRA involves identifying hazards and evaluating risks.
A unique perspective: What Is the Final Step in the Risk Identification Process
Why Is Important?
Risk assessments are crucial for creating awareness of hazards and risks. They help us identify potential dangers and take steps to prevent them.
A well-conducted risk assessment can determine whether a control program is required for a particular hazard. This is especially important at the design or planning stage to prevent injuries or illnesses.
Risk assessments also help us identify who may be at risk, including workers, cleaners, visitors, contractors, and the public. This is a critical step in creating a safe and healthy work environment.
By prioritizing hazards and control measures, risk assessments enable us to determine if existing control measures are adequate or if more should be done. This helps us stay on top of safety and health issues.
Here's a summary of the importance of risk assessments:
- Create awareness of hazards and risks.
- Identify who may be at risk.
- Determine if a control program is required.
- Prioritize hazards and control measures.
- Prevent injuries or illnesses.
- Meet legal requirements.
When to Do It
Before you start identifying hazards and risks, you need to know when to do it. A risk assessment should be done before new processes or activities are introduced.
You might be introducing a new machine on your shop floor, or implementing a new quality control process. Either way, a risk assessment is a must.
Before changes are introduced to existing processes or activities, including when products, machinery, tools, or equipment change, a risk assessment is necessary.
If this caught your attention, see: Hazard Identification Safety Risk Assessment Matrix
This could be as simple as upgrading your software or replacing a worn-out tool. Don't forget to assess the risks involved.
When new information concerning harm becomes available, it's time to reassess your risk management plan.
This could be a new study or research that reveals a previously unknown hazard. Stay up to date to stay safe.
You should also do a risk assessment when hazards are identified.
This might be a near-miss or an incident that highlights a potential hazard. Don't wait until it's too late.
Before working in a new environment, a risk assessment is a good idea.
This could be a new office, a construction site, or even a different floor in your building. Be aware of the potential hazards.
When new information on hazard controls or good practices becomes available, it's time to review your risk assessment.
This could be a new regulation or a best practice that's been developed. Stay informed to stay safe.
Before performing maintenance or commissioning of equipment, a risk assessment is required.
Consider reading: Time at Risk
This is a critical step to ensure the safety of your staff and the public.
Before completing routine or non-routine tasks, a risk assessment should be done.
This includes tasks like cleaning or repairs. Don't skip this step.
When the legislation requires a risk assessment to be done, you must comply.
Check your local regulations to see if a risk assessment is mandatory in your industry.
Planning and Strategy
To plan for a risk assessment, you need to define the scope of your assessment, which means being specific about what you're assessing, such as the lifetime of a product or the physical area where work takes place.
The resources needed for a risk assessment should be identified, including any training required for a team of individuals to carry out the assessment.
You should also determine the type of risk analysis measures to be used and how exact the scale or parameters need to be in order to provide the most relevant evaluation.
A comprehensive preparedness guide, such as the Comprehensive Preparedness Guide (CPG) 201, can provide valuable guidance for conducting a Threat and Hazard Identification and Risk Assessment (THIRA) and Stakeholder Preparedness Review (SPR).
Here are the key steps to consider when planning for a risk assessment:
- Scope of the assessment
- Resources needed
- Type of risk analysis measures
- Stakeholders involved
- Relevant laws, regulations, and organizational policies
Planning Strategy
Planning a risk assessment is a crucial step in identifying and mitigating potential hazards. To do this effectively, you need to define the scope of your assessment, which could be a specific product, physical area, or type of hazard.
The resources needed for a risk assessment should be clearly outlined, including the training required for team members and the types of information sources to be used. This will help ensure that your assessment is thorough and accurate.
In terms of risk analysis measures, you need to decide on the level of precision required to provide a relevant evaluation. This could involve using a scale or parameters to quantify risks.
Identifying stakeholders is also essential, as they will be impacted by the outcomes of your risk assessment. This could include managers, supervisors, workers, and suppliers, among others.
Relevant laws, regulations, codes, or standards should also be taken into account, as well as organizational policies and procedures. This will help ensure that your risk assessment is compliant with all relevant requirements.
Here's a checklist to help you plan your risk assessment:
Required Documentation
Keeping accurate records of your risk assessment is crucial. It's essential to store assessments for a specific number of years, so be sure to check local requirements in your jurisdiction.
The level of documentation or record keeping will depend on the level of risk involved, legislated requirements, and any management systems that may be in place.
You should document the following aspects of your risk assessment:
- Conducted a good hazard review.
- Determined the risks of those hazards.
- Implemented control measures suitable for the risk.
- Reviewed and monitored all hazards in the workplace.
Methods and Techniques
There are various methods and techniques for hazard and risk identification. A risk assessment team should use their knowledge and experience to determine the best approach for each situation.
The basic qualitative method combines severity and probability parameters to produce a level of risk that is compared against pre-determined risk criteria. This method evaluates risk based on the inherent characteristics of the hazard without assigning a numerical value.
A risk matrix is a useful tool for evaluating risk, as seen in Table 2. This table shows the relationship between probability and severity and how a risk rating can be determined.
Here's a breakdown of the risk ratings:
Other qualitative risk assessment methods include hazard and operability (HAZOP) analysis and bowtie analysis.
See what others are reading: Portfolio Risk Analysis
Hira vs Hazop: Key Differences
HIRA and HAZOP are two methods that share many similarities, but they have some key differences. HIRA is considered more comprehensive with a focus on identifying hazards.
One notable difference is that HIRA is focused on identifying hazards, while HAZOP is more detailed in terms of assessing the risks. HAZOP focuses on observed deviations and potential for hazardous events in particular equipment and material within a system.
Reducing Driving
Reducing driving risks is crucial to stay safe on the road.
The most important step in risk management is finding ways to eliminate or reduce risks, so they don’t cause or contribute to crashes.
Checking the weather forecast before driving can help you prepare for potential hazards like fog or heavy rain.
In the scenario where an employee is scheduled to meet with a client across town, they check the weather and see that it’s overcast with a chance of fog.
Being aware of your surroundings is essential to anticipate and respond to unexpected situations.
The driver in the scenario can barely see in front of the vehicle when the fog rolls in, highlighting the importance of staying alert and focused on the road.
Reducing Using Hierarchy of Controls
Reducing risks using the Hierarchy of Controls is a straightforward process. The Hierarchy of Controls is a step-by-step approach to identifying and controlling hazards in the workplace.
To start, it's essential to understand the different levels of control, which include Elimination, Substitution, Engineering, Administrative, and Personal Protective Equipment (PPE). Each level of control has its own steps to reduce driving risk.
For example, in a road safety scenario, the employee is driving faster than the speed limit to make up for lost time. To reduce this risk, we can consider the following steps:
By applying the Hierarchy of Controls, we can identify the most effective way to reduce the risk of accidents on the road.
Identifying and Assessing Risks
Identifying and assessing risks is a crucial step in the hazard and risk identification process. To identify hazards, you should look at all aspects of the work, including routine and non-routine activities, and consider the knowledge, experience, training, and education of the individuals performing the work.
Incidents, near-misses, and hazard reports should also be examined to identify potential hazards. Additionally, consider the groups of people that may have a different level of risk, such as young or inexperienced workers, persons with disabilities, or new or expectant mothers.
A risk assessment should be conducted to determine the likelihood and severity of harm associated with each hazard. This can be done using a risk matrix, such as the one shown in Table 2 or Table 3, which rates probability and severity to determine the overall risk.
The risk assessment should also consider the current controls in place and determine if they are adequate. If not, further measures may be needed to reduce the risk. Field-level risk assessments can be used in dynamic and changing work environments to identify, assess, and manage hazards and risks in real-time.
A table, such as Table 4, can be used to document the field-level risk assessment, including the step/task description, hazards, risk, priority, current controls, and recommended controls.
Here is an example of how to document the field-level risk assessment:
This table helps to organize the information and ensure that all hazards and risks are considered and documented.
Sources
- https://www.ccohs.ca/oshanswers/hsprograms/hazard/risk_assessment.html
- https://roadsafetyatwork.ca/resource/tool-kit/hazard-identification-and-risk-assessment/
- https://www.fema.gov/emergency-managers/national-preparedness/goal/risk-capability-assessment
- https://www.ors-consulting.com/hazard-identification-and-risk-assessment-hira
- https://blackmoresuk.com/5-step-approach-to-hazard-identification-and-risk-assessment/
Featured Images: pexels.com